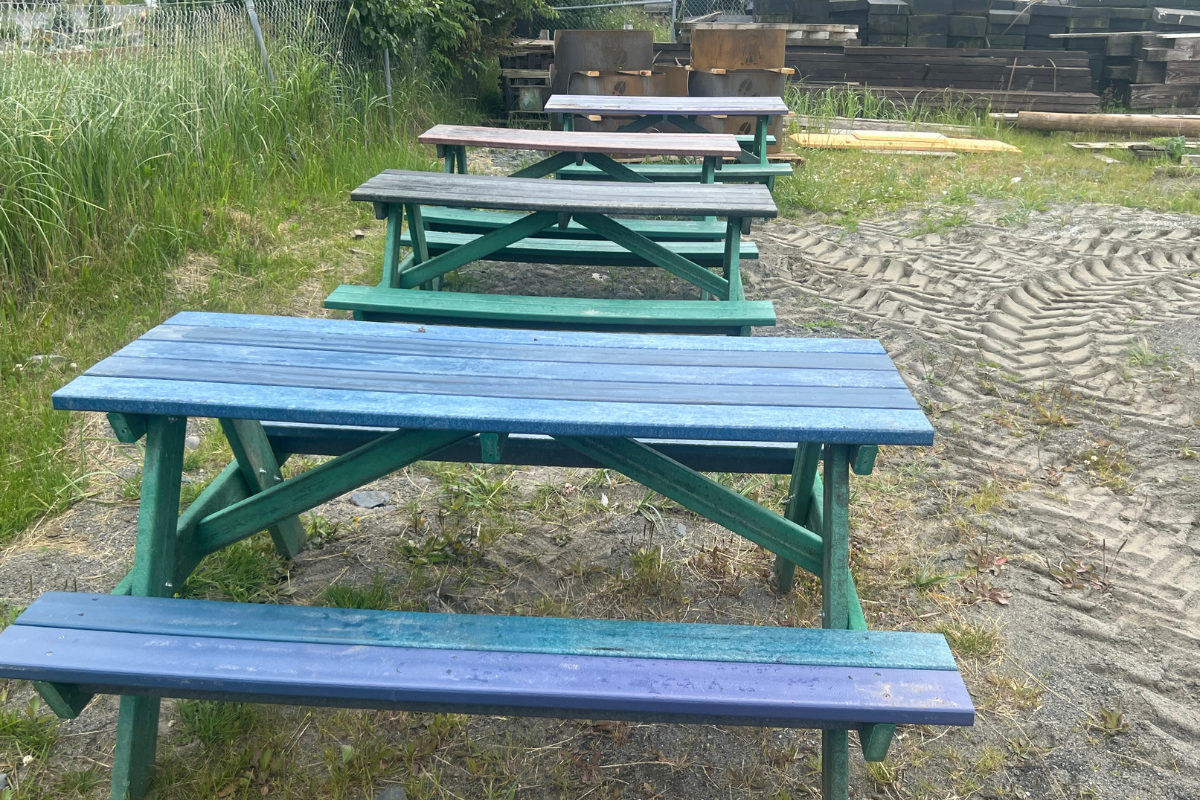
Grizzly Wood is made of 100% plastic waste, which limits color options but holds up well to the state’s harsh climate. | Courtesy of Alaska Plastic Recovery
A small company in Alaska is lending the state’s resourcefulness and ingenuity to creating composite lumber and addressing coastal plastics pollution.
Alaska Plastic Recovery uses PET, HDPE, LDPE and PP sourced from both post-consumer and post-industrial streams to create plastic lumber aptly named Grizzly Wood. The company will use other plastics under the #7 resin code – “if it works,” according to Rachell Murphy, the company’s director of sales and marketing – but in general it sticks to the more common plastic grades.
The company collects its plastics from the community, said Murphy. Post-consumer material is sourced via beach cleanups – marine debris especially in coastal communities – and drop-off locations.
“A lot of people love being able to drop off their plastics,” Murphy said. In Alaska, many companies charge for recycling and ship the materials to the lower 48 states, often by barge, she said. Alaska Plastic Recovery aims to repurpose plastic within the state instead.
Owner Patrick Simpson grew up in the fishing community of Cordova, Alaska, seeing all the plastic on the beach. He wanted to find a way to not only get rid of the plastic pollution but also reuse it within the state, Murphy said.
Alaska Plastic Recovery uses only recovered plastic in its composite boards, eschewing binders, additives and fillers such as sawdust, seen in lumber from such companies as Trex and Azek.
“It’s purely plastic, which is part of why the boards are so colorful,” said Murphy. “Some people are like, ‘I don’t want a bright green deck!’ Particularly with post-consumer plastic, it’s hard to guarantee a color when you’ve got so many various types.”
Nevertheless, the company has been experimenting with color, mixing red and green HDPE pipe-thread protectors in different proportions to make brown lumber. The thread protectors are sourced from the state’s North Slope oil production, Murphy said.
Mobile production
The state’s isolation limits transport options, so the company often brings its services to various communities, an approach with several benefits, Murphy said.
“One thing we’re doing differently is putting our equipment into 20-foot containers, so we can take it to coastal communities with a lot of plastic on their beaches,” she said. “So we can process and produce dimensional lumber on site, and avoid shipping costs.”
For example, a 53-foot trailer will move equipment to Haines – a town of about 1,700 residents more than 700 miles southeast of the company’s headquarters – for a month-long project in the fall, she said.
“We choose communities based off of their interest,” Murphy said. “And since Haines is on the road system, that made it easier.” Due to the harsh terrain, some Alaska communities are accessible only by plane or boat.
After approaching communities to gauge interest, the company considers funding availability, since logistics are so expensive.
“Some communities are really on board, and others are more hesitant, so we will come back to them in a year or so. Or they want to make sure we know what we’re doing (before they commit),” Murphy said.
The hyperlocal approach can bring other advantages too. Although the company currently has a crew of only about five people at its Palmer plant – all born and raised in Alaska – in the future the company wants to hire local residents to help with production during their stay in the community.
In Homer, more than 250 miles from Palmer, the company recently completed a trail project. The Homer Trails Alliance ordered lumber and completed the construction themselves. The plastic lumber is ideal for the wet and muddy conditions found in the area, because of its less slippery surface as well as its durability, Murphy said.
“Grizzly Wood is great for Alaska. You don’t have to stain it, don’t have to worry about rot, and it has a nice grip so it’s not slippery in wet coastal areas,” Murphy said.
Although decking projects are bigger in scale, picnic tables are the most popular item for both businesses and residential orders, Murphy said.
Each 2×4 weighs 16 pounds, and the company uses six 2x4s and 12 2×6 boards for each picnic table it produces. This results in a 400-pound table, which also is about how much plastic it takes to produce it, Murphy said.
The company has worked with municipalities as well as boroughs – the state’s version of a county – and even federal agencies, Murphy said.
So far in 2024, the company has processed more than 36,000 pounds of plastic, Murphy said. This is more than twice the amount for all of 2023, which was 16,000 pounds.