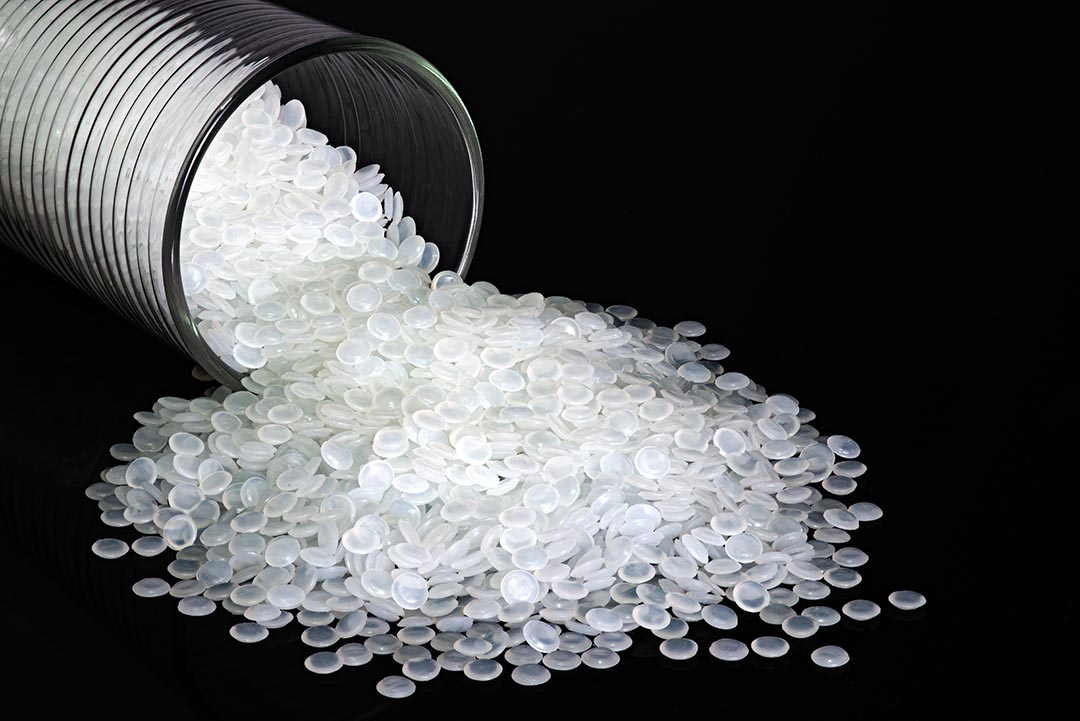
After multiple mechanical issues over the past year, the recycled PP resin startup is feeling optimistic. | Praethip Docekalova/Shutterstock
The PureCycle PP processing plant in Ironton, Ohio, has produced more than 1.1 million pounds of resin pellets since restarting May 30, according to the latest company update. CEO Dustin Olson elaborated on the progress in an interview.
The total represents the highest monthly yield since the high-purity PP extraction plant first started producing resin in June 2023, CEO Dustin Olson said in a press release. At full capacity, the facility is expected to produce 107 million pounds of virgin-quality resin annually.
Most of that total was produced between May 30 and June 10, the company said in the press release. During the rest of June, PureCycle was working to start up the system to remove co-product two, or CP2, and as a result lowered run rates.
CP2 consists of solid material removed from the feedstock and includes other plastics – primarily PE – as well as talcum powder and other additives from when the material was originally formed into objects, according to Olson in a company video from early 2024.
The plant began a planned shutdown in early April to address reliability issues and improve resin quality. Although PureCycle had expected the outage to last two to four weeks, its mid-May restart was interrupted by a storm-related power outage.
Until mid-June, the plant had been using a feedstock lower in PE, then switched to a feedstock with a higher concentration of PE, to utilize upgrades made during the April outage.
Higher capacity for co-product removal means the company could handle more contaminants in its post-consumer feedstock, which would help lower input costs and improve profit margins.
“We’re fairly agnostic as far as what type of feedstock we buy and use,” Olson told Plastics Recycling Update. “This gives us more feedstock flexibility as well as pricing power.”
Olson said most of what PureCycle feeds the plant is post-consumer waste, versus cleaner, more expensive post-industrial material.
“The consumer wants the PC waste because they want to know that what they throw out to the curb goes into a high-quality product,” he said.
Looking ahead, Olson said PureCycle traditionally buys post-consumer PP bales, or No. 5. However, bale quality varies – from 60% to 95% PP content – and the company watches that content very closely, he said.
PP is among the least mature of recycling commodities – colloquially, the redheaded stepchild, Olson said. Of the 180 billion pounds of virgin produced globally, less than 10% is recycled, he said, because there hasn’t been a good recycling solution. But providing the capacity to use the material incentivizes MRFs to be able to recover more of the polymer, which encourages consumers to put more PP in the waste stream, he added.
“PP is so versatile, and used in so many applications, because it’s low cost, and the lightest plastic on the planet,” he said. “But its [wide range of] reusability makes it harder to recycle.”
“PureCycle provides a no-compromise solution for the customer, and uses a wider spectrum of feedstock. That puts us into a position to let that ‘redheaded stepchild’ grow up into something beautiful.”
PureCycle refers to the Ironton facility as a purification plant. It uses solvents in a physical process to filter out contaminants such as PE from the post-consumer feedstock.
Shaky start
The Ironton facility has had its share of stops and starts, both figuratively and literally. The plant reached mechanical completion in Q2 2023, then in June 2023 produced its first pellets.
In November, PureCycle delivered its first commercial shipment of resin to Formerra, which serves as the primary authorized distributor of PureFive virgin-quality resin.
In the same month, the company said the plant had a leak that would need repair. Although in early December PureCycle said the plant had restarted, only two weeks later an update indicated another issue had developed, requiring a shutdown.
As a result of the mechanical issues, PureCycle was unable to meet the Dec. 31 bondholder deadline to produce 4.45 million pounds of pellets in a 30-day period, the company said at the time.
In February, the company delayed its Q4 financial update by about a week, citing the closing of its purchase of municipal bonds. The bonds replaced the company’s Pure Plastics Term Loan.
Then in April the plant underwent the planned shutdown to fix existing issues and upgrade co-product extraction equipment.
Rapid expansion
PureCycle is using lessons learned from the Ironton plant to inform its second U.S. plant in Augusta, Georgia. However, during a quarterly earnings call in late May 2024, Olson declined to provide a timeline for either the Augusta plant or a joint venture with SK Geo Centric in South Korea.
“Our first priority is to get Ironton up and running correctly,” he told Plastics Recycling Update. “Second is to integrate learnings from Ironton into the overall project, third is to ensure that the engineering performance is very high and fourth is to focus on implementation and growth projects.”
The JV with SK will be PureCycle’s first PP recycling plant in Asia, and SK announced in November 2023 that it had started construction for the plant, scheduled to be complete in late 2025.
PureCycle also announced it would build its first PP recycling facility in Europe at the Port of Antwerp in Belgium. The most recent update on the project in August was that pursuit of permits was continuing and was expected to be complete by late 2024.
The Belgium plant is expected to have an annual capacity of 59,000 metric tons, or 130 million pounds. The site can expand to support up to four lines with an anticipated combined capacity of approximately 240,000 metric tons per year.
PureCycle also has announced plans to build a new PP recycling plant with Mitsui in Japan. In August the company said it expected to execute its joint venture with Mitsui in Q4 2023, but this was the most recent update.