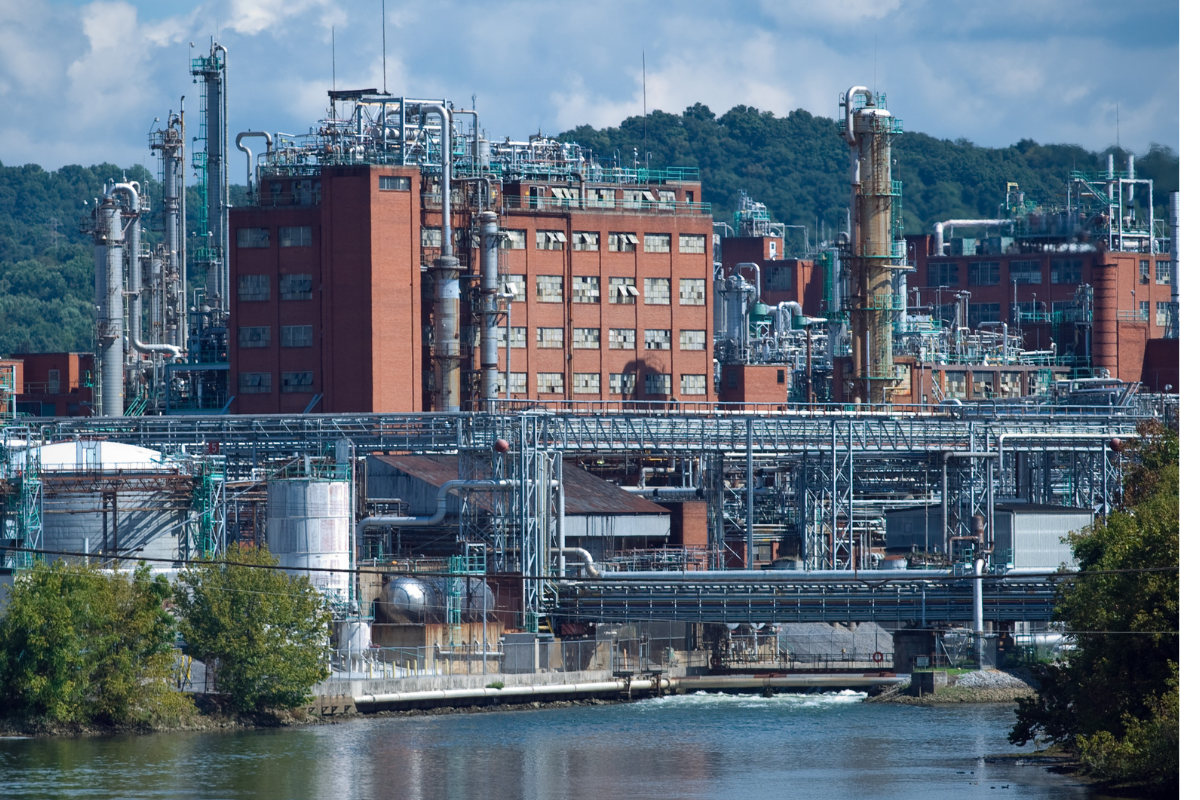
Eastman’s upcoming Kingsport, Tenn. plant was initially estimated to cost $250 million over two years, but recent financial filings suggest the price tag has crept upward. | William Griffith/Shutterstock
The CEO of Eastman Chemicals said today’s low PET prices are slowing negotiations over contracts to sell chemically recycled PET to brand owners, but he remains confident that recycled-content mandates and Eastman’s technological advantage will push the deals over the finish line.
Kingsport, Tenn.-based Eastman Chemical is building one of the world’s largest methanolysis plants at its headquarters location. The facility will use a depolymerization technology to break down post-consumer polyester scrap into chemicals that Eastman will use to produce new plastics.
CEO Mark Costa said he expects the company to start selling products from the plant around the end of the year. Next year, the company estimates earnings before interest, taxes, depreciation and amortization (EBITDA) of roughly $75 million from the project.
“We are also excited about the progress on our circular economy initiatives, including our target to produce material and realize revenue around year end from our Kingsport, Tennessee, methanolysis facility,” Costa stated in a press release.
He and other executives provided new details on the project in recent financial disclosures and a conference call with investors. Although the company isn’t disclosing the project’s costs, capital spending numbers suggest the price tag has increased since the project was first announced. Participants on the call also commented on how market conditions are affecting off-take agreement negotiations with brand owners, which include PepsiCo.
Capital spending in the hundreds of millions
When it was first announced in early 2021, the methanolysis plant was estimated to cost $250 million over two years and have a capacity of 100,000 metric tons at full build-out, making it “one of the world’s largest plastic-to-plastic molecular recycling facilities,” according to Eastman.
The company has also announced plans to build a similar plant in France and a third one somewhere else in the U.S.
During a July 28 Q&A call with investors, Greg Riddle, vice president of investor relations at corporate relations for Eastman, said the company isn’t disclosing the capital cost for the Kingsport project at this time.
But filings suggest it will cost a lot more than previously planned. According to the company’s recent quarterly financial disclosure, Eastman spent a total of $413 million on capital expenditures during the first six months of 2023, up 67% year over year. The spending was primarily for the Kingsport methanolysis plant “and other targeted growth initiatives and site modernization projects.”
During the call, William McLain, Eastman’s chief financial officer, said the company increased its estimated capital spending for the year from $700 million to $800 million.
Eastman has estimated its French methanolysis plant will cost $1 billion.
The plant was initially expected to be on-line by the end of 2022. In prepared remarks before the recent Q&A phone call, executives said substantial progress has been made speeding up construction in the last several months.
The company has been producing its chemically recycled PET, branded as part of the Eastman Renew product line, at a pilot plant on-site over the past two years. That plant uses a higher-cost glycolysis depolymerization process, which Eastman called a “bridge technology.” A number of brand owners have been using the chemically recycled plastic in their products.
Market conditions slow contract negotiations
During the call, Costa said global demand remains strong for the recycled-content products to be produced in Kingsport. One of the major companies that is interested in using Eastman’s chemically recycled PET from its methanolysis plants is PepsiCo.
Costa also noted that converting letters of interest from brand owners into signed purchasing contracts takes time, and current low prices for virgin and recycled PET aren’t helping.
“Like Pepsi, it takes a long time to negotiate these. They’re very complicated contracts,” Costa said. “And the current market conditions, I would say, are sort of slowing those discussions down a little bit. So, if you’re looking at the PET market, whether it’s VPET or RPET, those market prices have come off in a pretty significant way, which is purely just the story of everything else in the current macro, right?”
He added that demand for PET beverage bottles is down, and bottled water producers continue to lightweight their packaging. Additionally, he noted, a lot of RPET goes into carpet and other textiles, and demand is down in those markets as well.
He insisted, however, that Eastman is targeting applications where “mechanical recycling doesn’t really work,” including 100% recycled content products. “So while regulatory requirements may be only 25% in 2025, a lot of brands have set targets for some key applications to be 100% recycled content. And to maintain quality, they’re not going to be able to do that with mechanical,” Costa said.
He said the company remains confident the contracts will be signed, noting, “The engagement is high, and the regulatory requirements, especially in Europe, are going to require people to have recycled content.” He said mechanical PET reclaimers simply aren’t able to double their capacity between now and 2025 to meet the government minimum-recycled-content mandates for 25% RPET content in bottles.
“So, we feel like we’re in a good position, and working really productively with our customers and we’re aiming to have those contracts done by the end of the year,” he added.
For its next U.S. plant, Eastman is considering three sites, Costa said. While engineering work continues, company officials are working to lock down federal and state incentives to locate in the locations. Eastman anticipates announcing the location by the end of 2023.
“We feel great about our partnership with Pepsi as a significant base load customer in that project,” Costa said.
More stories about technology
- RIT researchers develop AI-based textile recycling system
- Industry nuance is key in adopting emerging technology
- Google, Dow partner on AI to identify recyclables