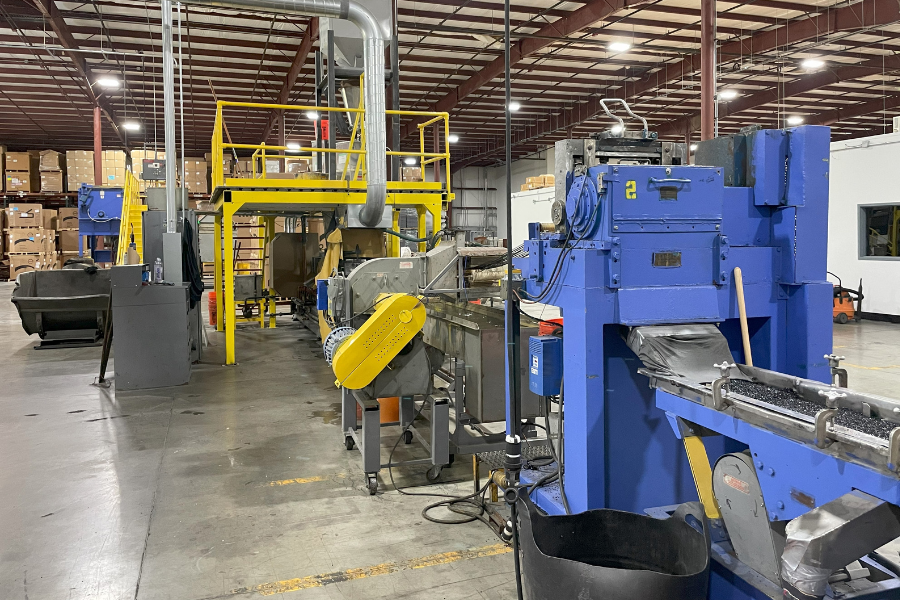
Polymer Resources has grown its Rochester, N.Y. facility to nearly twice its previous size, with plans to expand even further. | Courtesy of Polymer Resources
A Northeast U.S. compounder’s recent capacity upgrades represent part of an effort over the next two years to double the amount of recycled-content products it sells, an executive explained.
Farmington, Conn.-based Polymer Resources, a compounder of engineering resins, recently purchased another twin-screw extruder and additional processing equipment, in addition to making building upgrades that increased its manufacturing space.
In an interview with Plastics Recycling Update, Scott Anderson, president and chief operating officer for the company, described the project as providing needed production capacity growth, particularly for the company’s recycled-content line. Today, the recycled portfolio makes up less than 10% of overall sales by weight, he said.
“We see that growing, really doubling, over the next two years or less,” Anderson said.
Adding extrusion equipment
In business for over half a century, Polymer Resources has compounding facilities in Farmington and Rochester, N.Y., producing PC, ABS, PC/ABS, PBT, PPX grades and other resins for a variety of durable goods markets. The company uses virgin plastic, post-consumer material and production scrap, bringing in flakes, pellets, end-of-life or damaged plastic parts, and molder purges, often sourcing material from customers.
Scott Anderson
Before this recent upgrade project, Polymer Resources’ Rochester plant, where most of the recycled-content offerings are produced, held a shredder, grinder, metal separation equipment and three single-screw extruders. Polymer Resources bought a Leistritz twin-screw extruder and installed it at the Farmington plant. It moved an older Coperion twin-screw extruder from Farmington to Rochester. Additionally, the company installed a loading conveyor with metal detection in Rochester. The loading conveyor “improved ergonomics, safety and output capacity,” Anderson said.
Finally, the project expanded the footprint of the Rochester facility from 35,000 square feet, divided between two buildings, to 60,000 square feet in one building, according to a press release. That provides more space for compounding and grinding operations, storage, a laboratory and offices.
Forward-looking expansions
The site changes also give Polymer Resources the ability to add another 100,000 square feet in the future, as demand dictates, the release notes. A key feature of the new building is a soundproofed, 3,250-square-foot room for grinding and shredding the post-industrial and post-consumer scrap.
Anderson said the company implemented a much higher level of hearing protection inside that room. The soundproof room protects employees working outside that area from noise.
All told, the project, which was completed in just over a year, increased Polymer Resources’ total production capacity by about 40% between both facilities, said Anderson, who declined to disclose the capacity. Without divulging the exact cost, he described the investment as being between $1 million and $5 million.
Polymer Resources launched its full sustainable product offering in the last year. Products within that portfolio are made with over 50% recycled content, Anderson said.
Polymer Resources is undergoing the UL testing process to achieve certification for PC and PPX recycled-content grades. Several customers have already committed to purchasing the recycled-content grades once those approvals are obtained and the products are available, Anderson said.
Anderson said the need to “support our new sustainable portfolio and the growth that we need for that” was one driver of the expansion project. Other motivating factors were the need to increase overall capacity and the desire to change how buildings on site are occupied and used.