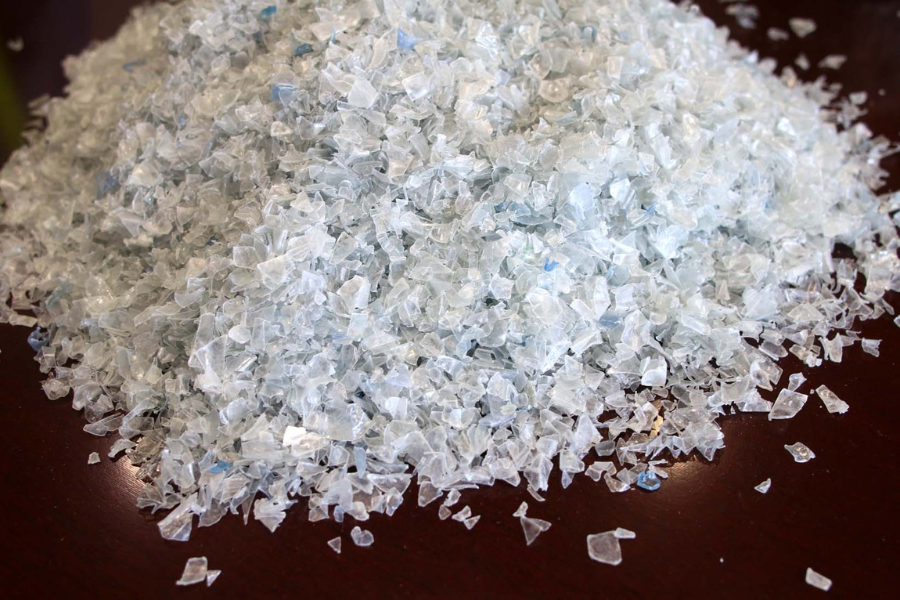
Much like the FDA does in North America, the EFSA evaluates which materials can be used in food and beverage packaging. | Jared Paben/Plastics Recycling Update
A European food safety panel has given the green light to a couple dozen companies seeking to use Bandera, Erema, Polymetrix and Starlinger recycling technologies to produce food-grade RPET.
Over the past eight months, the European Food Safety Authority’s (EFSA) Panel on Food Contact Materials, Enzymes and Processing Aids (CEP) gave the OK to two dozen applications. In every case, the CEP decided the technologies in the applications are able to produce food-grade flakes, pellets and sheets for use in 100% RPET food and drink packaging.
In the European Union, recycled plastics can only be used in food and beverage packaging if they’re first reviewed by the EFSA for safety. In that way, the EFSA serves the same role the FDA does in North America.
Twice a year, Plastics Recycling Update covers the CEP’s opinions. The most recent roundup was published in January 2023. The following are CEP determinations that have been published since the last roundup.
Erema technologies get the green light
On March 9, the panel approved two applications to use Vacurema Prime technology for PET recycling. The applications came from Creative Recycling World of Saudi Arabia and Loreco Plast Recyclage of France.
In the Vacurema Prime process, hot caustic washed and dried flakes are crystallized and decontaminated under high temperature and in a vacuum in twin batch reactors. Then, the reactors alternate feeding flakes into a continuous reactor using high temperatures and a vacuum. Finally, the flakes are melted in an extruder, solid contaminants are filtered out, and the plastic is extruded into pellets.
The CEP has also approved a number of applications to employ the Erema Basic technology for PET recycling. On Jan. 24, the panel approved applications from Steinbeis PolyVert of Austria and Zhenjiang Ceville Recycled Fiber of China. Earlier, on Nov. 15, 2022, the panel approved an application for this technology submitted on behalf of Poly Recycling of Switzerland.
In the Erema Basic process, hot caustic washed and dried flakes are fed into a reactor with a rotating device. There, exposed to heat and a vacuum, they are crystallized and decontaminated. The flakes are then moved into an extruder, where they’re melted and the melt is filtered and extruded into pellets.
The pellets resulting from both the Vacurema Prime and Erema Basic processes can be used to produce 100% RPET packaging for a variety of drinks and foods. The products could be filled in the containers either via a hotfill process or not, and long-term, room-temperature storage of the product and packaging is allowed.
One exception to the above is that Steinbeis PolyVert application is proposing to skip pelletizing and instead convert the melt from the extruder directly into sheets, which would then be used to create 100% RPET thermoformed packaging for food.
Combining Erema and Polymetrix tech
Four applications are proposing to combine PET recycling technologies supplied by Erema and Polymetrix. The combined technology is called Vacunite.
The CEP approved all the applications. They came from Renovapet of Spain (March 9 approval), Steinbeis Polyvert of Austria (also a March 9 approval), Plastipak Iberia of Spain (Jan. 24 approval) and Poly Recycling of Switzerland (Oct. 27, 2022, approval).
The Vacunite offering includes both the Erema Basic process and the Polymetrix SSP V-leaN equipment. The Erema Basic process, which is described above, produces crystallized pellets, which are then processed in Polymetrix’s solid-state polycondensation (SSP) equipment. Specifically, the crystallized pellets are preheated under vacuum and gas flow for a specific time. Then they’re continuously fed into a countercurrent reactor, where they’re exposed to heat, a vacuum and gas flow for a set time. Finally, the plastic is pelletized.
In all cases above, the resulting pellets could be used to make 100% RPET packaging for a variety of foods and drinks, using either hotfill processes or not, for long-term storage at room temperature.
Bandera PURe 15 process approved
A PET recycling technology from Italian company Bandera received the nod from the CEP as well.
On March 9, the panel OK’d applications from Italian companies Aristea and Roboplast.
As with the other technologies, the input is hot caustic washed and dried flakes. The CEP opinion document redacts details of the Bandera PURe 15 process, but a schematic shows that it involves a hopper, four microwave devices, a heating chamber, two reactors, a vacuum pump and two buffer silos.
The output is flakes, which can be converted into 100% RPET packaging for a variety of food and drink types, except for mineral water. The packaging is OK for hotfill and long-term storage at room temperature.
A dozen-plus Starlinger applications OK’d
Over the past eight months, the CEP has approved 13 applications to use different Starlinger recycling technologies.
Most of those were for the Starlinger iV+ technology. Specifically, CEP approved the following applications to use iV+ on Nov. 14, 2022: Alef Recycling Company of Nigeria, Duy Tan Plastic Recycling of Vietnam and rPET Aviv Shalam of Israel.
On March 9, the panel approved another six iV+ submittals from the following companies: Commercial Plastics Company of Myanmar, Akmert Iplik San. Ve Tic. of Turkey, Royce Universal of Thailand, Basatli Boru Profil Sanayi ve Ticaret of Turkey, General Plastic of Slovakia and Green PET Recycling of Israel.
In Starlinger’s iV+ process, hot caustic washed and dried flakes are further dried and crystallized in a reactor under high temperature and air flow. Then, the flakes are fed into an extruder, where they’re heated, exposed to a vacuum and then pelletized. The pellets are then sent into a continuous reactor, where they’re crystallized under high temperature under atmospheric pressure. Finally, the crystallized pellets are preheated in a reactor before they are introduced into a semi-continuous solid-state polycondensation (SSP) reactor, which is running under vacuum and high temperature.
In all cases, the resulting pellets can be used in 100% RPET food and drink packaging for all types of foods and beverages, including mineral water and other beverages. The packages, which can be filled via a hotfill process, are suitable for long-term storage at room temperature.
Earlier, on Oct. 27, the CEP approved an application from EcoBlue Limited of Thailand to use Starlinger’s direct iV+ technology. Similar to iV+, this process directly processes the flakes into pellets without first crystallizing them. Then, the pellets are processed in the same way they are through the iV+ technology.
On Oct. 27, CEP approved an application from Ester Industries of India to use Starlinger’s recoSTAR PET FG technology. Through this process, hot washed and dried flakes are sent into a continuous reactor, where they’re heated and crystallized at high temperature and exposed to a preheated inert gas. Then, the crystallized flakes are sent into another reactor where they’re further processed, although the details in this step were redacted in the CEP opinion document. Finally, the flakes are continuously fed into an extruder, where they’re melted and pelletized or used for in-line production.
The pellets produced can be used in 100% RPET food and drink packaging, including for water. The packages, which can be filled via a hotfill process, are suitable for long-term storage at room temperature.
Finally, the CEP on Dec. 7 greenlit applications to use the Starlinger deCON technology from Petecoflex of Bulgaria and Derchia D.C. Plastics of Taiwan.
In this process, the washed and dried flakes are preheated in batch reactors up to the temperature of the next step, the SPP. There, the flakes are exposed to high temperatures and a combination of vacuum and gas flow. In this process, the output is decontaminated flakes.
For both applications, the output can be used for 100% RPET packaging for food or drinks, including mineral water, soft drinks and beer. The packages can be filled with either a hotfill process or not, and they are suitable for long-term storage at room temperature.