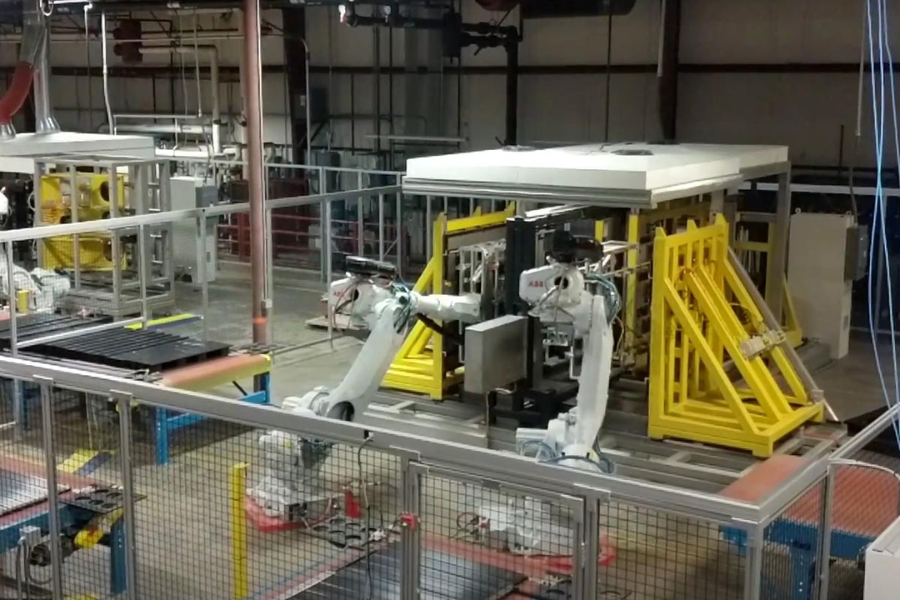
At its new location, Greystone plans to produce pallets made of 100% recycled resin. | Courtesy of Greystone Logistics
Greystone Logistics, which recycles tens of millions of pounds of recovered polyethylene a year into pallets, has acquired a pallet production operation in Indiana.
The Tulsa, Okla.-headquartered manufacturer announced in an April 24 press release that it purchased the assets of Paradigm Plastic Pallets in Jasper, Ind. The assets include extrusion lines and pallet manufacturing equipment, including material-handling robots.
“This acquisition will provide Greystone with access to world class manufacturing support, a deeply researched and developed product line, an experienced and robust nationwide sales network and highly respected leadership,” Warren Kruger, Greystone’s CEO, stated in the release. “We are very excited to be able to add plastic extrusion capability to the Greystone family of pallets and are looking forward to a very bright future for the product line.”
Executives declined to disclose the purchase price, although they said it was financed entirely through a bank loan with the company’s existing lender.
With its manufacturing plant in Bettendorf, Iowa, Greystone recycles roughly 50 million pounds of polyethylene each year into 100% recycled plastic pallets, which are used by distributors and retailers, including Walmart, Molson Coors, J.R. Simplot, Diageo and others, to store and move their products. Another major customer is pallet leasing company iGPS.
The company’s recycled feedstock includes hundreds of thousands of damaged plastic pallets a year, as well as post-industrial plastics and clean post-consumer flakes purchased from other reclaimers.
Producing different pallet sizes
Paradigm manufactured pallets in Jasper not through injection molding but through a hollow-profile extrusion process. The products include styles and sizes that Greystone doesn’t currently make through its injection molding machines.
The release notes that Paradigm Pallets have been approved for use by Toyota, Honda, Berry Global, Sonoco and other major companies.
“We’ve had a lot of requests for large pallets, custom-made pallets. We really weren’t in that world. And this allows us to do some things,” Kruger told Plastics Recycling Update in an interview.
During an April 17 conference call with investors, Kruger explained that Paradigm spent $3 million-plus to install its automated line at the end of 2019 to produce pallets for Toyota, but the outbreak of COVID-19 early in 2020 affected the company and it “could never get back on its feet.”
Paradigm’s investors had directed Paradigm to liquidate the equipment, which Greystone was able to buy at a discount, he said. Uline has asked Greystone to produce the oddball-sized pallets that could be manufactured in Jasper, he said.
In the interview, Kruger confirmed Greystone will produce 100% recycled plastic pallets in Jasper. Ron Schelhaas, plant manager for Greystone, confirmed the company has access to enough recycled plastic supply to make recycled plastic pallets at the new Jasper location.
Greystone is also installing two new injection molding machines at an unnamed partner’s plant in Palmyra, Mo. Each will produce up to 200,000 pallets per year.
Lower recovered plastic prices give profit boost
In other recent Greystone news, the publicly traded company on April 14 released its quarterly financial report for the quarter ended Feb. 28, 2023. The document noted that lower recovered plastic prices last year helped boost profitability, even as sales revenues slowed.
Specifically, for the nine months ending Feb. 28, the company’s sales totaled $44.6 million, down 16% from the same period the year before. But gross profit was $6.0 million, up 17%. That was because the cost of sales was lower, “primarily the result of declines in the cost of raw material coupled with increases in the average price per pallet sold.”
“Management continues to strive for additional reductions in the cost to produce pallets due to anticipated savings from scheduled increases in the capacity for internally refining unprocessed recycled plastic,” the report notes.
Greystone announced last year plans to purchase a new shredder and pelletizing system to allow it to rely less on purchasing recycled plastic from outside reclaimers. That goal was to reduce the company’s feedstock costs and boost profitability.
During the conference call, Kruger explained that Greystone competes with pipe manufacturers, a large market, when it comes to buying recovered PE. “We have always been a bottom-feeder in terms of resin. We like to buy material and then clean it up ourselves, grind it, granulate it and BB it ourselves.”
In the interview, Kruger said the additional grinding and extrusion equipment, which is being installed in Bettendorf, has mostly been delivered. He estimated it will be up and running within 90 days.
He also touched on recycled plastic pricing over the past two years.
The February 2021 freeze in Texas shut down plastic production capacity, which drove prices higher for virgin and recycled resins, Kruger explained during the investors call. From February 2021 through August 2022, recycled resin costs rose from 15 cents per pound to 30 cents per pound, he said. The company was forced to raise its prices for pallets accordingly, which affected sales to customers, including Walmart and iGPS, he said.
“Now [pricing] has stabilized and recycled plastic has come down, thankfully,” he said during the interview.
However, In the investors call, Kruger noted that Greystone is maintaining its higher pricing, providing a profit margin benefit.