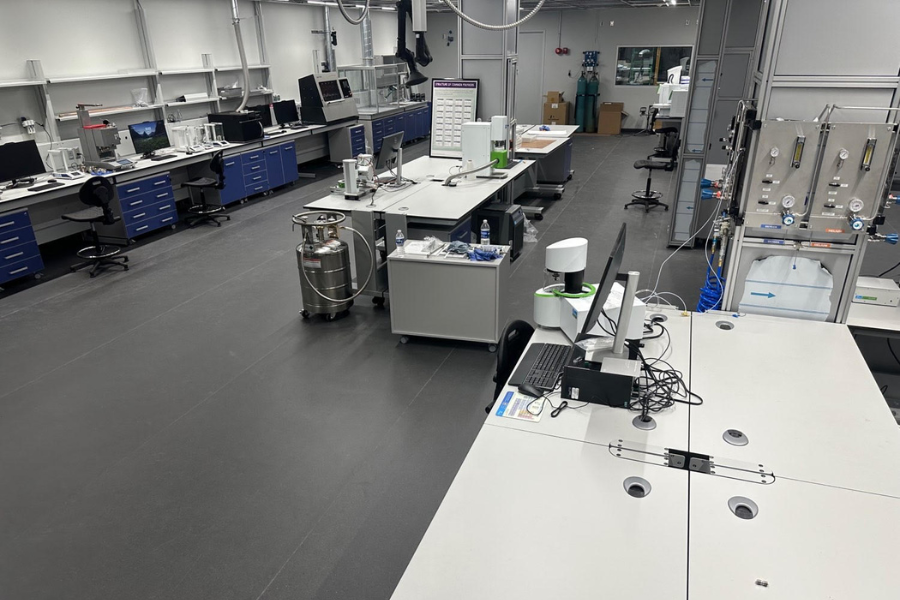
The new $2.5 million plastics recycling laboratory at PRI’s Indianapolis compounding facility. | Courtesy of Plastic Recycling Inc. (PRI)
Plastic Recycling Inc. is set to build out a fully outfitted laboratory and install extrusion lines that will boost recycling capacity by 60 million pounds per year. It’s also expanding its e-plastic sorting capabilities.
In an interview, leaders at Plastic Recycling Inc. (PRI) discussed the significant investment at the reclaimer’s 550,000-square-foot Indianapolis compounding facility, where PRI pelletizes post-consumer PP, ABS and PS.
Separately, PRI plans to spend another $2 million installing a line in Spartanburg, S.C. to shred, wash and sort plastics from electronics, electrical appliances and vehicles. That line will be modeled off the e-plastics system that the company installed at an Indianapolis facility a couple of years ago.
In an interview with Plastics Recycling Update, company officials explained that the $10 million project will allow PRI to quickly produce compounds that meet OEM specifications for use in automobiles and electronics. With the new lab, which will be staffed by 10 to 12 people, PRI will be able to perform 90% of the testing required to qualify recycled resin for use by auto OEMs, testing the thermal, mechanical, chemical and optical properties of the plastic, said Marco Meloni, PRI’s chief operating officer.
“Having all this testing capacity internally will allow us to move and to go very fast forward,” Meloni said.
“This will reduce our time to market in developing new products dramatically, because we’ll be able to get everything in maybe three, four months, when maybe normally it would take one year,” he added.
Boosting extrusion capabilities
PRI’s compounding plant currently has roughly 125 million pounds per year of extrusion capacity, said Brandon Shaw, marketing manager for PRI. The company has purchased two additional lines – one with a single-screw extruder and the second with a twin-screw extruder – boosting capacity by about 60 million pounds per year, or about 50%.
The lines, which cost about $3.5 million each, will include automatic feeding systems, pre-blenders, post-blenders, automatic screen changers and more, Shaw said. He said Celectric is supplying the extruders, BHT is providing the conveyors and dosing systems, and Ettlinger is supplying the melt filtration.
Meloni explained that the systems will include dosing equipment that will automatically blend different feedstocks, additives and fillers to produce consistent resins that meet customer specifications. The feedstock will include PP, ABS and PS from electronics and other sources.
“We are effectively bringing the technology of virgin compounding into recycling,” he said.
The extrusion lines will sit on multiple floors. Construction of a mezzanine level to hold equipment will begin in April, and the extrusion lines are slated to come on-line around mid-summer.
The project, which started last August, also includes building out a $2.5 million lab, Shaw said. That lab is 90% completed right now.
Meloni said the lab’s R&D and feedstock and finished product testing capabilities will be unrivaled in North America. Shaw said the lab “is going to be unbelievable.”
The lines have been designed to maximize automation in terms of controls and moving material, helping PRI save money and compete with Asian reclaimers who enjoy lower labor costs, Meloni said.
The company is also going through a reorganization that aims to increase the pounds processed per staff hour. That effort, which includes staff training and equipping existing staff with new technologies, will allow PRI to run the new lines and lab without hiring additional employees, Meloni said.
Growing e-plastics sorting capacity
Feedstock for the new compounding equipment will include flakes produced by PRI’s 120,000-square-foot scrap processing facility in Indianapolis. The e-plastics processing system there can produce roughly 25 million pounds of washed, sorted flakes a year.
PRI’s investments in its compounding capabilities prepare it to handle greater volumes of e-plastics feedstock in the future. PRI is one of several companies pushing to increase domestic recycling outlets for e-plastics and reduce exports to Asia, especially Malaysia, where many e-plastics are recycled.
“We’re putting the extrusion in to satisfy what we’ve already invested in but to also be prepared for more feed streams coming to us in the future,” Shaw said.
In the next four to six months, PRI plans to install and bring on-line a plastics sorting line at a building in Spartanburg, S.C., Shaw said, adding that PRI bought the building about a year and a half ago. That roughly $2 million investment will include size-reduction equipment, float-sink tanks, flake sorting, electrostatic separation and more. Processing plastics from consumer electronics, electrical appliances and auto shredder residue, that line will be capable of producing about 25 million pounds per year.
“There’s a lot of supply and opportunity down there,” Shaw said.
Joshua Barrick, who oversees business development at PRI, said many electronics recycling companies in the U.S. and Canada want to send their e-plastics to domestic outlets. They’re also feeling pressure from certification standards and changes to the Basel Convention to eschew e-plastics exports.
But sometimes they don’t believe the domestic capacity exists, and often pricing still lures them to export the material, he noted.
“I think a lot of them say they want to do the right thing, but it comes down to the money is still there over in Malaysia, let’s say,” Barrick said. “So we’re kind of battling with that.”
He said PRI has the plastics sorting and compounding capabilities and knowledge that some other aspiring domestic e-plastics outlets have lacked. “Some of the places that try to open, try to do it domestically, they don’t have all the pieces,” he said.