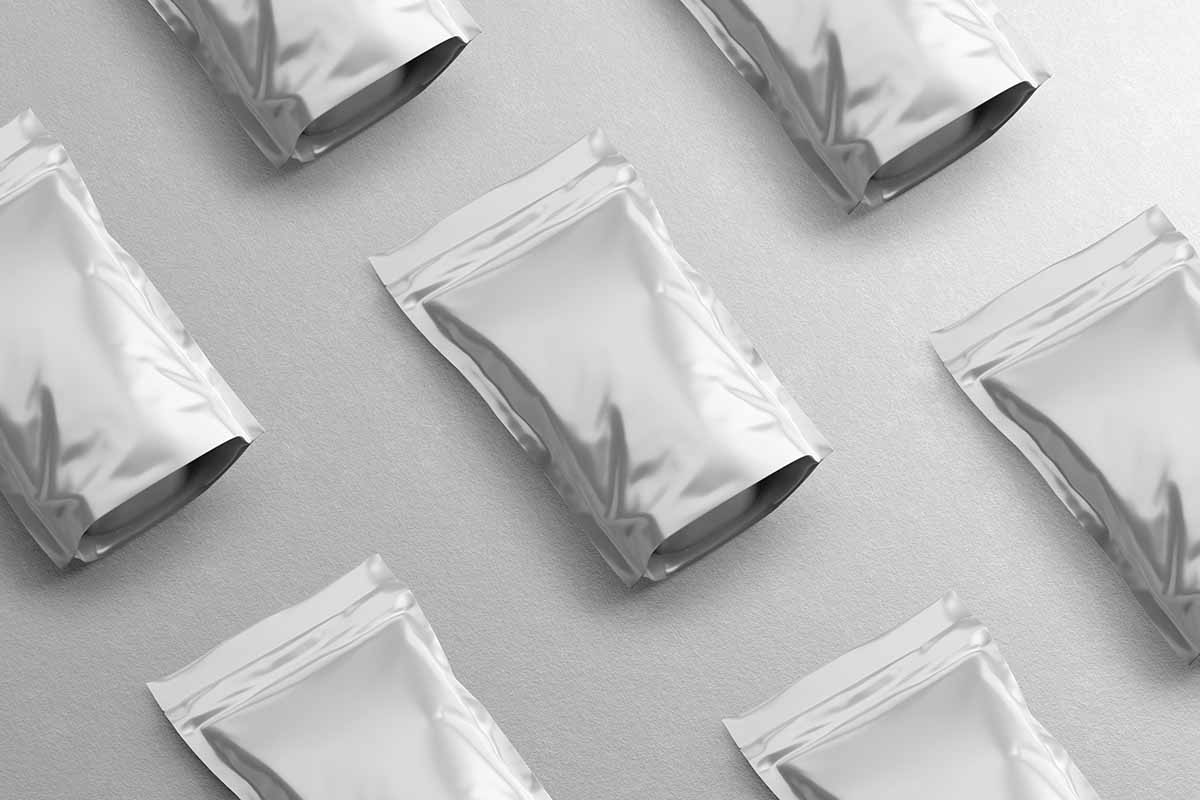
Collecting a wide variety of film packaging curbside and sorting it at a materials recovery facility (MRF) can deliver big benefits, according to a report on a years-long pilot program. | Tiffy Studio/Shutterstock
Collecting a wide variety of film packaging curbside and sorting it at a MRF can deliver big benefits, according to a report on a years-long pilot program.
The Materials Recovery For the Future (MRFF) project was spearheaded by the American Chemistry Council (ACC) and was supported by a variety of plastics packaging stakeholders. The effort ran flexible film recycling trials at the J.P. Mascaro TotalRecycle materials recovery facility (MRF) in Birdsboro, Pa. going back to 2019.
The third final project report, prepared by consultancy RRS and covering efforts from 2020 to 2022, found that TotalRecycle’s pilot flexible plastic packaging curbside recycling program in Pennsylvania diverted over 2.7 million pounds of material from landfill, reduced labor needs and created cleaner paper bales.
The report was released March 9 and follows previous reports prepared by RRS that covered results of automated sorting technologies, the pilot stage of the project and end market testing.
Susan Graff, vice president of global corporate sustainability at RRS, said in a press release that there’s “a significant opportunity for MRFs, flexible packaging manufacturers and the paper industry to work together on equipment upgrades to increase the quantity and quality of PCR supply for post-consumer recycled content products.”
The primary market for the mixed film bale, called rFlex, is roof coverboard, the report noted, though trials with Charter Next Generation (CNG) found that it could be used to produce blown films with a moisture management additive. However, the resin and the finished film had an odor. CNG suggested further trials with additives to address color, appearance and odor.
RRS noted in the report that “once threshold quantities of production in the range of three to five million pounds annually are reached at the MRF, a wash line to reprocess rFlex for film production will become economically justified.”
Using a variety of tools on MRF line
The aim of the project was to capture all film and flexible packaging except extremely small packages (those smaller than 2.5 by 4 inches). It also excluded anything made of PVC.
Ten communities served by TotalRecycle were invited to put the material in their curbside carts. Those communities together covered 56,900 households.
Because film material generally ends up with paper in single-stream MRF, optical sorters, air flow controls, collection hoods and other peripherals on fiber lines were used to do a positive film sort.
Van Dyk Recycling Solutions installed optical sorters on each of TotalRecycle’s three fiber lines to eject film from fiber at high speeds. A fourth optical sorter cleaned up the resulting film stream by ejecting the remaining fiber after the three lines converged. A flex/rigid separator was also installed.
In 2020, a human-staffed manual quality control station was added after the automated sorting to pick any missed film.
In all, that equipment configuration has the capacity to auto-sort 6.2 million pounds of film per year at a facility the size of TotalRecycle, according to the report. In 2021 and 2022, TotalRecycle produced about 1 million pounds of rFlex per year, about 16% of the system’s capabilities.
“The main reason TotalRecycle is not producing greater tonnage is a shortage of curbside carts in the communities served,” the report noted, along with COVID-19 disruptions and labor shortages. In 2021, the MRF “operated with significantly reduced staffing levels, 25-30% of normal staffing,” the report added.
The report noted that the COVID-19 pandemic also slowed the pace of development in manufacturing end markets.
RRS performed several tests to check feasibility and performance. An August 2020 RFID test found an average capture rate of over 70% for the targeted film materials. Some packages had much higher rates, such as retail carry bags, which hit 90% by the end of the pilot.
“However, smaller packages were much harder for the system to capture, and they were more affected by maintenance issues, weather and other unknowns,” the report stated.
In 2022, RRS conducted a system assessment in collaboration with The Recycling Partnership that concluded that labor shortages had affected overall equipment maintenance, though the film recovery equipment “appeared to be working relatively well.”
On the re-manufacturing side, the use of rFlex generated greenhouse gas savings of about 25% compared to products made with virgin materials, the report noted.
In addition to ACC, project supporters included Amcor, Chevron Phillips Chemical, Dow, Johnson & Johnson, LyondellBasell, Mars and Procter & Gamble, as well as the Association of Plastic Recyclers, the Canadian Plastics Industry Association, the Flexible Packaging Association and the Plastics Industry Association.
More stories about film
- Brand owners lead initiative for scalable film, flex recycling
- APR, ReMA update bale specs for PE rigids, film
- NexTrex program boosts local film recovery efforts