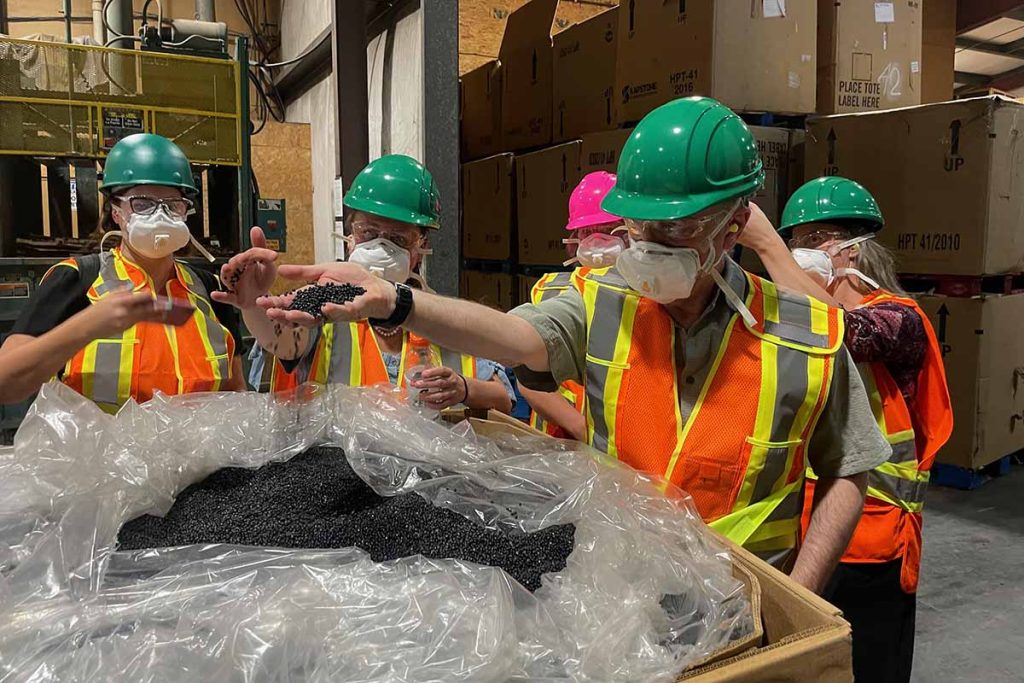
KC Recycling is heavily involved in recycling lead batteries, which are roughly 4-5% polypropylene by weight. | Courtesy of KC Recycling
A British Columbia recycling company has struck a supply deal allowing true closed-loop recycling of polypropylene from lead batteries.
KC Recycling, which recycles lead-acid batteries from vehicles and scrap electronics, signed an agreement to supply 100% recycled polypropylene (PP) pellets to lead-acid battery manufacturer East Penn for molding into new battery casings. The scrap plastic comes from batteries shipped from East Penn Manufacturing to KC Recycling, which is located in Trail, British Columbia.
“We recognize that as stewards of the circular economy – even if it’s perhaps not the easiest way to make a buck … – it is the right thing to reclaim the battery plastic and send it to them,” Pete Stamper, CEO of KC Recycling, told Plastics Recycling Update.
Lead-acid batteries are roughly 4-5% PP by weight. Last year, KC Recycling received a grant from the government of British Columbia to help fund a project to install washing, extrusion and pelletizing equipment, allowing the company to process PP flake into higher-quality pellets for sale into various markets.
Initially delayed by vaccination and cross-border travel restrictions, that line came on-line in March 2022, Stamper said. Since then, the company has been shipping out roughly 100,000 pounds a week of 100% recycled black PP pellets.
Meanwhile, East Penn, which is headquartered in Pennsylvania, has been expanding its production capacity at plants in Iowa and Texas. One of the largest lead-acid battery producers in North America, East Penn sells batteries under the Deka brand.
East Penn’s growth plans provided the opportunity for KC Recycling to supply plastic from the company’s batteries to the Iowa facility, where the PP is molded into battery casings, Stamper said. A little less than half of the PP pellets coming off KC’s production line are now traveling to East Penn’s Iowa plant, he said.
In terms of scrap supply, East Penn has long sent used batteries from its distribution centers in Western Canada to KC Recycling, which is the only lead-acid battery recycler north of Los Angeles and west of Minneapolis, Stamper said. Last year, KC started taking the company’s batteries from Washington and Oregon, as well.
Expanding supply and finding other markets
KC has been working to expand its plastics recycling activities.
KC also sells recycled PP to manufacturers for molding into paint buckets, plastic liners and other products, with some amount still sold to compounders. The company recently started supplying its PP to a plant pot manufacturer in Washington state, Stamper said.
KC Recycling is looking at other scrap sources, including children’s car seats and paint buckets.
“In the coming years we expect to double or triple our production by incorporating new post-consumer plastic products such as car seats, paint buckets, and more lead batteries,” according to a company press release.
Car seats are made of roughly 40% PP. During recycling testing, KC’s industrial-sized electronics shredder, which is equipped with magnetic sorting equipment, was able to produce a clean stream of PP from car seats, Stamper said.
For supply, the company is exploring partnering with Canadian nonprofit group ATMO Recycling, which operates a collection program for car seats in Ontario and is interested in expanding the program to British Columbia, he said. In order to efficiently recycle car seats, KC would need to install additional infeed equipment, he noted.
A version of this story appeared in E-Scrap News on November 17.
More stories about challenging materials
- Unifi pushes for textile recycling progress
- PET Recycling Coalition doubles down on thermoforms
- RIT researchers develop AI-based textile recycling system