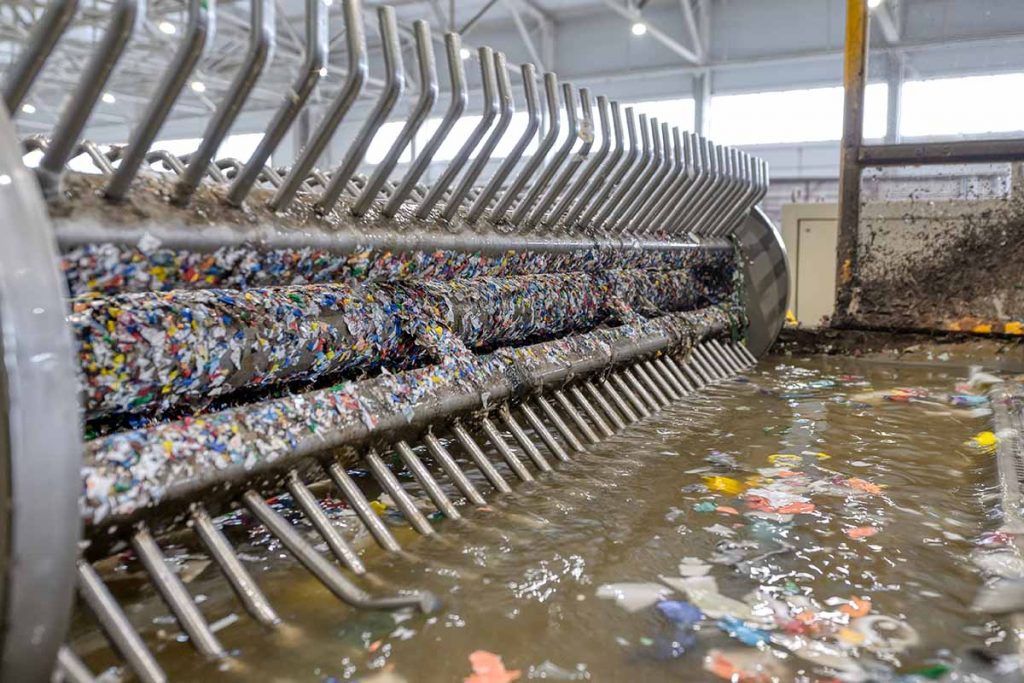
Three experts at a wastewater treatment system provider cover the myriad issues plastics reclaimers need to consider when shopping for a system. | Nordroden/Shutterstock
Wastewater treatment in plastics recycling
Recycling of plastics and other materials is becoming increasingly important worldwide. The industry is experiencing a boom, driven by laws and regulations that mostly apply at the national level. For this reason, existing recycling companies are planning to expand their capacities, new entrants into the recycling sector are no longer rare and companies from other sectors are discovering the recycling sector as another mainstay.
One component of the recycling process is the use of wash water, which is incorporated into two two phases of the recycling process. Recyclers often wash incoming material before processing it further. If the recycler shreds plastic into flakes to produce pellets, a second washing process is essential. Depending on the type of recycled plastic, the size of the plant or the washing process, different amounts of wastewater are produced – up to two cubic meters per metric ton of recycled plastic.
The following components can be mixed into the wastewater: fats and proteins from organic soiling, plastic abrasions, salts and sugars from residual liquids, printing inks, washing chemicals, cellulose fibers and adhesives from labels. This has an impact on two of the sum parameters used for assessing water quality: chemical oxygen demand (COD) and biochemical oxygen demand (BOD5). While the BOD5 can be as high as 12,000 milligrams per liter, the COD usually rises to 20,000 milligrams per liter. The pH value is similarly variable, usually between 6 and 14.
Thomas Leistner
The sodium hydroxide hot washing process is crucial for a high wastewater load and the associated effective cleaning performance. This process is usually used to rewash already crushed flakes with washing water at a temperature of at least 80 degrees Celsius (176 F), which, with the addition of caustic soda, frees the flakes from their contaminants. The usual consumption is about 30 liters (7.9 gallons) of caustic soda per metric ton of recycled material. Remaining cellulose fibers swell due to the caustic soda and thus detach from the recycled material.
There are many ways to further utilize the wastewater produced:
One such option is known as indirect discharge, meaning wastewater is cleaned before being discharged into a public sewer system. The municipal wastewater treatment plant purifies the wastewater and then discharges it into a receiving body of standing or flowing public water. Reuse of the wastewater in its own cycle is thereby precluded.
An increase in capacity is not always possible. Although some municipal plants are generously designed and can therefore accommodate a larger influx of wastewater, the majority are already at their load limits, which is why some recycling companies are prohibited from indirectly discharging more wastewater.
Another option is direct discharge, where the recycling company discharges the independently treated wastewater into a receiving body of water, or into the natural environment if the company lacks sewer access. Discharge parameters are determined regionally by the relevant authorities or municipalities based on required wastewater purity. In this way, the recycling company saves on operating costs, as the fees for indirect discharge do not apply.
A third method of dealing with wastewater is to reuse it in the recycling process. Despite the availability of state-of-the-art treatment solutions, 100% reuse of wastewater is rarely achieved. The main reason for this is the concentration of dissolved and non-dissolved substances. Likewise, part of the water – around 5% – evaporates during the washing process. Therefore, a fresh water supply of at least 10% is necessary to maintain the smooth washing process.
Wastewater treatment is worthwhile for many companies
Sabine Düreth-Joneck
The European Commission, as part of its Green Deal initiative, released a set of values for recycling companies that want to discharge their wastewater into a receiving body of water. These are adaptable but binding for the recyclers. This gives them an indication of the level at which wastewater treatment must take place. By means of laboratory analyses, the relevant parameters of the wastewater can be determined and the treatment solution that is best suited for achieving the discharge requirements can be found.
If the recycling company expands its capacities, more wastewater is produced. However, if the municipal wastewater treatment plant is operating at full capacity, it is necessary to treat the wastewater in-house. The treated wastewater can either be reused in the company’s own cycle or discharged directly. Depending on the type of treatment plant, about 50% to 90% of the treated wastewater is suitable for reuse.
In-house power generation is an increasingly common topic among recycling companies, and special wastewater treatment processes offer ways to put electricity to good use. Solutions such as oxidation processes or reverse osmosis use electrical energy to produce particularly pure wastewater. With these processes, about 90% can be reused.
The provision of firefighting water is obligatory for recycling companies. This must be replaced regularly to prevent bacterial growth. A supply of treated recycling wastewater helps to keep storage tanks at the required level.
Factors to consider when installing a wastewater treatment plant
Because wastewater can vary greatly depending on the type of recycling, the size of the company and the processing procedure, the treatment plant must be adapted precisely to the customer’s requirements. A treatment plant manufacturer therefore needs to know several key pieces of information, such as flow rate, wastewater values, discharge parameters or location in the company. Recyclers should therefore make sure that the supplier requests this information in advance.
After pinning down the parameters above, plastics reclaimers must seek out products of the best possible quality. High-quality products are recognized by recycling companies through independent certifications, which can usually be found as downloads on the company website. The more certificates available, the better the cooperation with the testing institutes and thus the quality of the treatment plants.
Markus Mostegel
Next, reclaimers should consider what advanced technologies are available to them. Biological treatment processes and dissolved air flotation (DAF) are long-tested solutions for wastewater treatment, but there is also ongoing research and thus further development in this area. Recyclers should also pay attention to newer treatment processes such as oxidation, ultrafiltration or reverse osmosis.
Another crucial consideration is laboratory analysis. Often the exact sum parameters, such as COD, BOD5, total suspended solids (TSS), nitrogen, phosphorus, chlorides or sulfates, are not known. Some manufacturers of wastewater treatment plants therefore offer analyses in their in-house laboratories. In the laboratory, tests are carried out that provide information on the treatability and suitability of precipitants and flocculants. These allow the DAF system to be designed to precisely fit the facility. For this, only a wastewater sample of a few liters is necessary. The recycler receives the exact values of their wastewater in written form, usually in combination with an offer for a suitable treatment solution based on the lab’s analysis.
Energy efficiency is yet another important factor to take into account. If a plant consumes very little electricity, it is not only easy on the recycler’s wallet, but also evidence of advanced technology and the use of state-of-the-art treatment processes. Some producers have consumption certificates and can thus certify energy efficiency.
Not every wastewater treatment plant has to be associated with a purchase, and leasing offers can help get a project off the ground. Plant manufacturers often offer leasing deals for six months, a year or two years. These are usually available more quickly because they do not have to be built first. In individual cases, the leased plant is available for purchase should the recycler be satisfied with the treatment result.
Even after the plant has been constructed or leased, recyclers must not forget about repairs. A wastewater treatment plant needs care and maintenance at regular intervals. In some cases, an employee of the recycling company is responsible for this. Although this person receives all the information from the plant manufacturer during installation, he or she should be available around the clock, if possible, to respond to issues that arise during operation.
Finally, plastics reclaimers should look for guarantees. To ensure that recyclers buy a wastewater treatment plant risk-free, they should look for long-term guarantees in all areas. Ideally, producers offer warranties of up to 15 years on selected parts.
Thomas Leistner, Sabine Düreth-Joneck and Markus Mostegel work for PPU Environmental Technologies, based in Bayreuth, Germany. Leistner is marketing and sales assistant, Düreth-Joneck is head of the F&E Department and Mostegel is the technical manager at PPU. The company has supplied over 40,000 private, municipal and industrial wastewater treatment systems in 50 countries.
The views and opinions expressed are those of the author and do not imply endorsement by Resource Recycling, Inc. If you have a subject you wish to cover in an op-ed, please send a short proposal to news@resource-recycling.com for consideration.