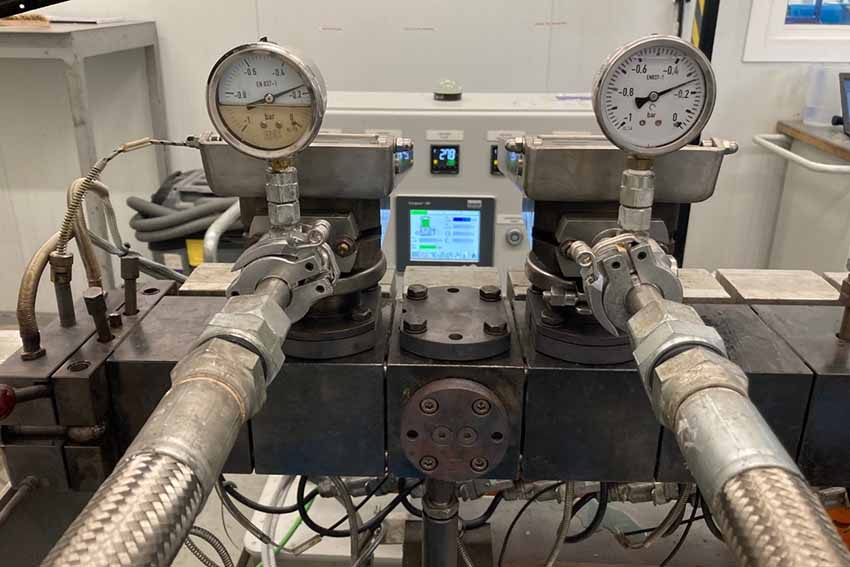
An expert explains why twin-screw extruders hold distinct technological and business advantages over single-screw extruders.
It is clear that the current plastics situation is affected tremendously by an environment in which the circular economy is a megatrend and reducing the environmental impact of products is strictly monitored.
As part of this trend, using materials with a lower environmental impact, such as recycled plastics, will become necessary for most industries over the next few years either as a result of regulations, the initiative of companies with more environmental awareness or the demands of a society with a growing commitment to environmental issues. In addition, regions such as Europe, which are highly dependent on raw materials from developing countries that often experience geopolitical problems, must speed up their circular economy policies if they do not want to lose competitiveness to other players on the world stage due to supply and price issues. Against this backdrop, the increased use of recycled plastic is an inevitable development and both economies and productive processes will have to adapt to using more of this recycled material and overcoming the technological challenges involved.
Evolving away from from single-screw extruders
Recycled plastic has traditionally been a material whose low cost took precedence over all other factors and whose fields of application were of low added value. It was even perceived as negative by the general public. These conditions affected the recycling process, which aimed to be as efficient as possible and produce recycled material at the lowest possible cost. This meant that most of the equipment used to convert post-consumer plastic into pellets consisted of single-screw extruders, which were efficient and not too expensive. They provided good results in commodity plastics such as the polyolefin, polyethylene (PE) and polypropylene (PP) families by focusing on the change in format from shredded or flake to pellet, which is easier to transport, handle and process by injection or extrusion.
Luis Roca
However, as clients demanded modified and higher-quality polyolefins using options such as inorganic fillers, the single-screw extruders started having difficulties mixing, eliminating volatile compounds and controlling total productivity. The same thing happened when working with more technical materials. At this point, recyclers considered making the leap to co-rotating twin-screw extruders and, with time, recyclers became compounders. This was a normal and logical process for many Spanish and other European companies in the sector, and single-screw extruders were gradually replaced with co-rotating twin-screw extruders.
Compared with single-screw extruders, co-rotating twin-screw extruders have the advantages of accepting most formats and having an increased mixing capacity, higher productivity, greater degasification capacity and enhanced business potential due to their ability to obtain compounds and work with a wider variety of materials.
These characteristics and the aforementioned change in mindset about recycled plastic have enabled co-rotating twin-screw extruders to start being viewed as the equipment of choice by plastic recycling companies, given that better-quality recycled materials are increasingly required in non-commodity polymers. New demands even include improving the properties of these materials so they are almost as good as virgin raw materials, thus giving rise to new concepts such as upcycling (recycling to improve properties).
These quality improvements must be focused on the increased use of post-consumer materials in sectors of higher added value, such as the automotive, electrical-electronic, construction and consumer goods industries.
Addressing limitations in recycled materials
The main problems found by users of recycled materials (besides the lack of a steady supply in terms of quantity and quality) are:
- Deficient mechanical properties.
- Inadequate rheology.
- Possible contamination and odors.
- Problems arising from the presence of different plastics and mixed plastics
Co-rotating twin-screw extruders have demonstrated their capacity to address these problems, thus making them an indispensable tool for driving the increased use of recycled materials that European industry needs.
The mechanical properties of co-rotating twin-screw extruders make it possible to transform shredded materials of different bulk density while adding inorganic fillers, fibers and additives that can largely make up for the loss of properties associated with the degradation of post-consumer material. Moreover, thermal and UV restabilization can be combined in this process to significantly increase the final quality of the recycled material.
Rheology is another essential aspect of plastic processing. Due to the different grades of post-consumer scrap, being able to adjust the rheology to a specific melt flow rate is also very important. Because co-rotating twin-screw extruders use controlled degradation, they can adjust the melt flow rate in PP and polyamide. In highly viscous polymers such as HDPE, they are able to increase melt flow rates to levels that allow for problem-free reprocessing.
Recycled material from post-consumer waste may be exposed to many kinds of contamination. In fact, a number of solvents may have penetrated its matrix and later be released as volatile compounds, which are unacceptable in many applications. However, co-rotating twin-screw extruders, with their modular screw and sleeve design, have many devolatilization areas (up to four in some cases) compared with one area or none in single-screw extruders, which gives them greater odor-elimination capacity. Agents can also be injected to help extract volatile compounds and decrease odors from volatile organic compounds (VOCs) and fogging compounds (FOG), and further drive the use of post-consumer material in plastic sectors with stricter regulations.
Separating two different kinds of plastic is often very difficult, as in the case of multi-layer flexible films, but co-rotating twin-screw extruders are able to produce a blend due to their blending capacity from the addition of the most suitable polymer compatibilizers.
Co-rotating twin-screw extruders have no problem working with all plastic materials. They can easily accept, transport, melt and blend these materials, including everything from low bulk density films to shredded technical polymers and rubbers. This extends the potential recycling business and ensures very quick adaptation to the needs of different sectors.
These examples provide a clear picture of how the great versatility of co-rotating twin-screw extruders makes them a very valuable player in the new paradigm of high-quality plastic recycling. This capacity calls for extensive knowledge of the process (e.g. screw configuration and blend energies) and how it affects the plastic materials and additives selected.
Based on the needs of the plastics and recycling industry, AIMPLAS does research on the topics discussed above and offers industrial solutions that include reducing volatile compounds in compliance with automotive industry standards, improving the mechanical properties of waste electrical and electronic equipment (WEEE), adjusting PP and PE flows, reintroducing carbon and glass fibers in technical compounds, making plastics more compatible in multi-layer structures and devulcanizing rubber.
Luis Roca is the compounding leader at AIMPLAS, a plastics technology center based in Valencia, Spain.
The views and opinions expressed are those of the author and do not imply endorsement by Resource Recycling, Inc. If you have a subject you wish to cover in an op-ed, please send a short proposal to news@resource-recycling.com for consideration.