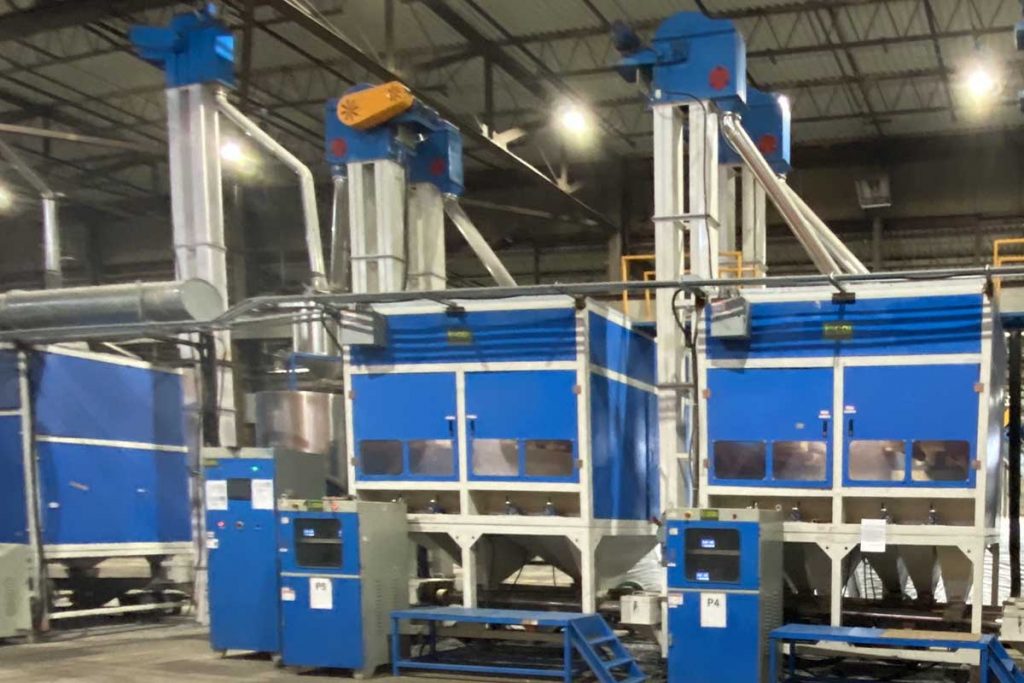
BoMET is one of a number of North American companies that saw that opportunity and are investing to expand their e-plastics processing capacity. | Courtesy of BoMET Polymer Solutions
BoMET Polymer Solutions is actively sourcing e-plastics from electronics recycling firms for the company’s Ontario processing facility, where it produces pellets and regrind for sale to manufacturers.
BoMET, which also operates an e-scrap recycling facility in Albion, N.Y., first announced the e-plastic processing project in 2018. There have been a number of hurdles along the way, and over the past year the company reorganized its expansion project, modifying some of the equipment that was planned for installation, among other changes.
In the last few months, the company began steadily processing scrap plastics from a variety of suppliers.
In an interview, Bo Zhang, CEO of BoMET Polymer Solutions, described the origins of the project and offered details on the equipment in use, e-plastic sourcing and future plans for the facility.
Facility opens as Basel controls take effect
The Brantford, Ontario BoMET facility is handling all major e-plastic resins, including ABS, PS and PE/PP. Exports of these e-plastics have been hampered by overseas import restrictions, including recent changes to the Basel Convention, an international treaty covering waste shipments.
Beginning this year, e-plastics, which are often sold as a shredded mixture of materials, are subject to new shipment restrictions under the Basel Convention. Generally speaking, scrap plastic loads that include mixtures of a variety of resins are subject to new notification requirements when exported. There are additional complexities – exports from the U.S. may not be allowed into certain countries, and the EU as a whole has banned the export of scrap plastic.
These factors have created turmoil for many recycling operations, including electronics recycling firms looking to move the plastic they recover from devices.
BoMET offers a North American outlet for those materials. The company has installed what Zhang described as a “comprehensive” system that includes eight float-sink tanks to sort e-plastics. The facility also has an electrostatic separation line, an optical sorter and two pelletizing lines, Zhang said.
The float system is capable of sorting 12,000 pounds per hour, and the facility is currently running two shifts, five days per week. BoMET is planning to scale up to three shifts in the near future, Zhang said. The company is also planning to add a shredding system to handle baled plastics recovered from CRT devices, as well as a near-infrared system to sort individual grey and white plastics.
The company produces finished pellets as well as regrind, and currently most of its customers are in the international market, Zhang said, although it is making a push to sell to local end users.
The processing facility is bringing in – and paying for – e-plastics from electronics recycling companies in Canada and the U.S., and it has received more inquiries for potential scrap suppliers of late, Zhang said.
“They are all looking for domestic solutions,” Zhang said.
BoMET also formed a supply partnership with Quantum Lifecycle Partners, a major Canadian e-scrap processor, which will use the BoMET facility as a domestic outlet for its e-plastics.
Additionally, BoMET is working with Shanghai Re-Mall, a Chinese polymer engineering firm that is helping BoMET navigate the overseas market for its products. The company has expertise on quality specifications that can help BoMET ensure its materials meet criteria for importing countries, Zhang said. For example, BoMET sends regrind or pellets to Shanghai Re-Mall, which analyzes them and can guide BoMET on specific attributes that need improvement, Zhang said.
The Brantford, Ontario BoMET facility is handling all major e-plastic resins.
International markets drive project
Well before the Basel amendment, the BoMET project was spurred by the growth in overseas import restrictions for recycled materials. This kicked off with China’s Green Fence initiative in 2013 and has expanded since then, with China’s National Sword effort in 2017 and an all-out ban on imported scrap plastic in 2018.
These restrictions hit the North American recycling industry hard, leaving many companies struggling to move materials they used to send to China. Electronics companies that handle e-plastics were no exception.
“With National Sword in place, we know we are going to lose a lot of business, but in the meantime we know with dramatic change there is opportunity,” Zhang said.
The company has been active in the metals recycling space for years, but those international changes led Zhang and other company leaders to look at the plastics space as an opportunity.
“With e-scrap plastic, in the last 25 to 30 years there is no such practice here, because automatically everything went to China,” Zhang said.
That’s largely due to the cost of setting up processing facilities in North America compared with China and Southeast Asian countries. Several key changes occurred in recent years to allow development of the BoMet e-plastics facility – in particular, the processing technology has progressed to become far less labor-intensive than even six or seven years ago, Zhang said.
The cost began to pencil out, and BoMET also developed a team of experts in the field to help create the Canadian facility.
“We have to balance the practice, the technology, the equipment and the manpower,” Zhang said.
BoMET is one of a number of North American companies that saw that opportunity and are investing to expand their e-plastics processing capacity. Other recent e-plastics processing projects were undertaken by Indianapolis-based Plastic Recycling, Inc., Ontario-based eCycle Solutions and Wisconsin-headquartered Universal Recycling Technologies.
The shift in where material is processed is leading manufacturers to consider moving their operations to be closer to the supply of feedstock, Zhang said. He said multiple manufacturers are already doing this, including producers of recycled-content products such as plastic pots for the garden industry. And he predicted this will be the case for manufacturers of other recycled-content products, including clothing hangers, plastic decks and more.
“They will be setting up plants in the States and in Canada, because the material supply is here,” Zhang said. “Their market is here as well.”
A version of this story appeared in E-Scrap News on February 4.
More stories about challenging materials
- Nova commissioning first US film recycling plant
- Industry groups form recycling alliance for PS
- Bans of some EPS take effect in California, Oregon