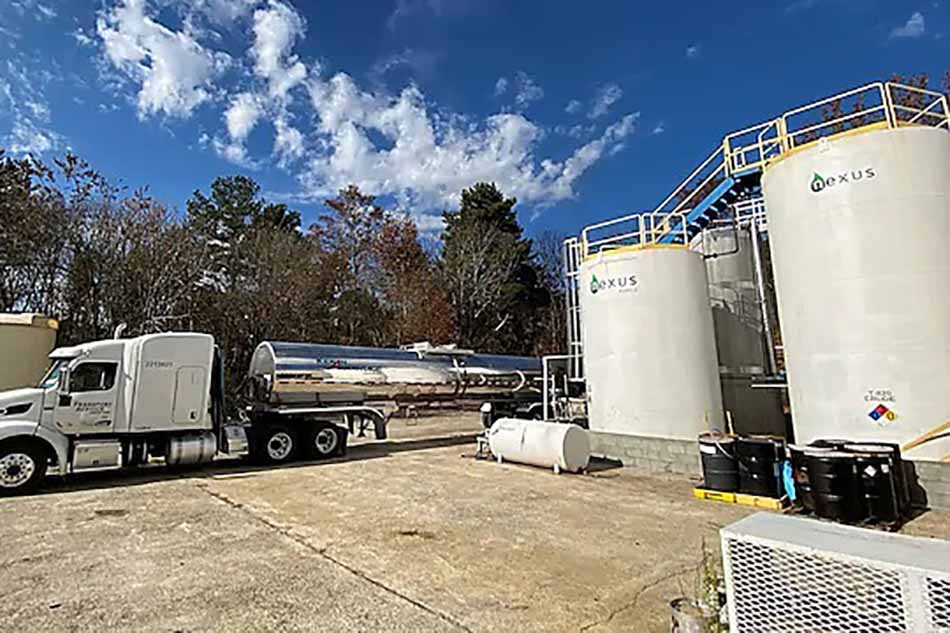
The CEO of Nexus Fuels told Plastics Recycling Update how his company uses its pyrolysis technology to convert the mix of post-consumer plastics collected at the curb into chemical and wax products. | Nexus Fuels
For the past two years, difficult-to-recycle plastics have been collected in Cobb County, Ga. through the Hefty EnergyBag program. A downstream processor recently described what happens to that material.
In an interview, Jeff Gold, CEO of Atlanta-based Nexus Fuels, described how his company uses its pyrolysis technology to convert the mix of post-consumer plastics collected at the curb into chemical and wax products. Among the companies buying the chemicals are Shell and Chevron Phillips Chemical (CPChem), which feed them into their plastic production plants.
“That’s exactly what’s happening with every drop of our material right now,” Gold said. “It’s being used to make new plastics.”
“That’s their selling point is to be able to say, ‘This plastic product was made with 100% recycled plastic material,” he added.
The EnergyBag program accepts a variety of household plastic items in orange bags collected at the curb, including multi-layer films, polystyrene foam, plastic utensils, straws and other materials. They’re sent to MRFs, where the bags are picked before they enter automated sorting systems. Then they’re shipped to different downstreams.
Across the U.S., the EnergyBag program, which is backed by Dow and Reynold Consumer Products, has signed up communities in Idaho, Georgia and Nebraska. Those programs have collected over 2 million pounds of material.
The program in Cobb County, which is an Atlanta-area jurisdiction that includes the city of Marietta, launched two years ago.
Need to pre-sort the materials
For the past year, bags from Cobb County have made their way to Nexus Fuels via a MRF operated by WestRock, a paper packaging producer. Gold explained that the first loads of EnergyBags came straight to Nexus Fuels, but the company found they contained high levels of contamination, including metals, PET bottles, even shoes and clothing.
To solve the problem, WestRock has an employee open the bags and presort them to remove obvious contaminants, Gold said. The usable material is transferred to gaylords, which are shipped to Nexus Fuels.
Contaminants still get through, including metal clips, chip bags with aluminized linings, and PVC items. But, generally, the quality has improved considerably, Gold said.
“In general, the material is very, very usable to us now,” he said.
Usable materials, which Nexus takes in for free, include multi-laminate films, PE films, PP and PS, Gold said, adding that Nexus tries to limit the amount of PS entering the system.
When shipments arrive, if they still contain visible contaminants, Nexus will perform a manual floor sort to remove obvious contaminants, such as paper items. Then, the material is shredded before undergoing a manual sort, followed by magnetic separation. Finally, it is shredded again and sent to the heated sections of the pyrolysis system, Gold said.
The EnergyBag materials get mixed in with feedstock from other sources within as far as a couple-hundred-mile radius of Atlanta, Gold said. Most of the other feedstock consists of lower-grade post-commercial and post-industrial films, along with some mixed rigids. The EnergyBag program provides a very small percentage of Nexus’s overall feedstock, said Gold, who called it “a drop in the bucket for us.”
According to a program spokesperson, in 2021, Cobb County stakeholders are hoping to achieve a milestone of 100 tons processed through the program.
From plastics to plastics
Nexus uses a pyrolysis technology, which involves heating material in the absence of oxygen, to break long-chain hydrocarbons into smaller chains. The process results in saleable wax and oil fractions. It also produces some amount of non-condensable gas, which is fed back into the system and burned to generate the heat needed for the pyrolysis reaction. The process also produces some amount of char, a waste product.
The wide-spec oil produced contains light and heavy fractions, Gold said. Because most crackers these days are designed to process natural gas, there aren’t many left that can handle a heavy liquid feed such as Nexus’s, Gold explained; however, Nexus’s partners have equipment that can efficiently process the oil.
Last fall, Nexus signed an agreement to sell 60,000 metric tons of pyrolysis oil to Shell over four years. Shell processes that oil, along with some amount of Nexus’s wax, into chemicals used to make new plastic, Gold said. Shell received International Sustainability and Carbon Certification (ISCC) Plus certification for processing pyrolysis oil into ethylene, pygas, propylene and butadiene at its Norco, La. steam cracker.
On Jan. 25, Nexus announced that the company has also signed an agreement to sell pyrolysis oil to Chevron Phillips Chemical (CPChem) for processing into new plastic at CPChem’s Baytown, Texas plant. Gold said he wasn’t able to disclose a tonnage figure for that contract. CPChem received ISCC Plus certification for converting pyrolysis oil to ethylene, HDPE and LDPE at the Baytown cracker. Nexus Fuels, itself, has also received ISCC Plus certification for converting mixed plastic scrap into pyrolysis oil.
More stories about technology
- RIT researchers develop AI-based textile recycling system
- Industry nuance is key in adopting emerging technology
- Google, Dow partner on AI to identify recyclables