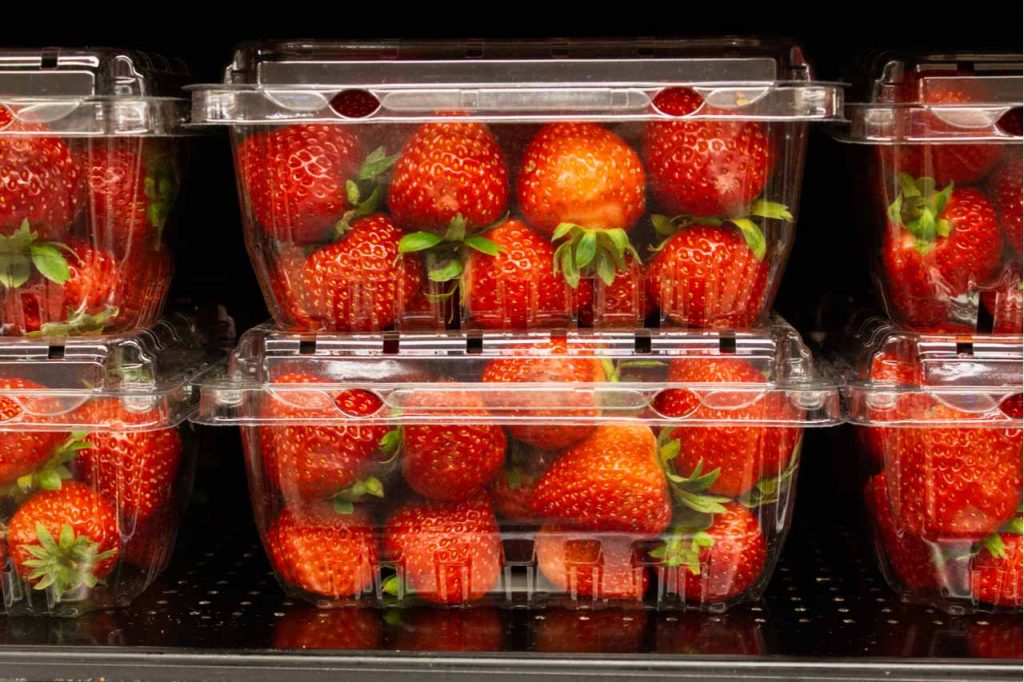
A group of companies recently received approval to use their recycling technologies to create recycled plastic for use in food packaging.| Dolores M. Harvey/Shutterstock
The European Food Safety Authority gave four companies approval to recycle PET into food packaging using Erema and Starlinger technologies. Meanwhile, an application from Veolia was rejected.
The Panel on Food Contact Materials, Enzymes and Processing Aids (CEP), which is part of the European Food Safety Authority (EFSA), issued five opinions on PET recycling processes in recent months.
In the European Union, recycled plastics and additives can only be used in food and beverage packaging if they’re first reviewed by EFSA for safety. Recycling companies submit applications to individual countries, which apply to the EFSA on their behalf. In all cases below, the German Federal Office for Consumer Protection and Food Safety submitted the applications on behalf of the companies.
The following is a semi-annual roundup of recent opinions from CEP. Plastics Recycling Update published its previous EFSA roundup in December.
Approval given for Starlinger technology
On Feb. 4, the CEP issued an opinion allowing Russian company PolyER to use Starlinger deCON technology to recycle post-consumer PET into flakes for use in bottles or thermoforms.
In the first step, scrap containers are processed into hot caustic washed and dried flakes, which are then pre-heated in batch reactors by a flow of hot gas. After that, the flakes are introduced into a solid-state polycondensation (SSP) continuous reactor, where they’re exposed to high temperature and a combination of vacuum and gas flow. That decontaminates them and boosts their intrinsic viscosity.
The resulting flakes can be converted into 100% RPET thermoforms or bottles for any type of food or drink, although trays are not intended to be heated in a microwave.
Erema basic technology gets nod
On Feb. 5, the CEP approved three companies to use versions of the Erema basic technology to recycle post-consumer PET for food-contact applications. It published approvals for three Germany companies: RE-PET, Buergofol and STF Recycling.
In each case, the input material is hot caustic washed and dried PET flakes from post-consumer containers. The flakes are continuously fed into a reactor equipped with a bottom-mounted rotating mixing device. They’re crystallized and decontaminated under high temperature and vacuum. Then, the flakes are fed into the extruder, where they’re melted under atmospheric pressure and solid contaminants are filtered. In the case of RE-PET and STF Recycling, the plastic will then be pelletized; in the case of Buergofol, it will be extruded into sheets.
The panel determined RE-PET’s recycled pellets can be used at up to 70% content in water bottles and up to 100% content in other product packaging, Buergofol’s sheets can be used to make 100% RPET thermoforms to hold food and drink (except drinking water) and STF Recycling’s pellets can be used in 100% RPET food and drink packaging.
Panel declines to OK Veolia application
On April 29, CEP published an opinion concluding that Veolia PET Germany had not submitted enough detailed information about its Veolia URRC process to demonstrate it produces PET flakes that are safe for food and drink packaging.
“Based on the information submitted to EFSA, the applicant has not demonstrated in an adequately performed challenge test or by other appropriate evidence that the recycling process is able to reduce contamination of the PET flake input to a concentration that does not pose a risk to human health,” the CEP wrote.
Veolia PET Germany applied to use its Veolia URRC process to recycle post-consumer food-grade PET containers into flakes. The technology was formerly known as “modified hybrid URRC UnPET,” according to the opinion, and the panel previously evaluated the technology, but the latest application includes modified operating parameters.
In the URCC process, scrap PET containers, mainly bottles, are processed into hot caustic washed and dried flakes, which are fed into the URRC technology. The process involves three main steps. First, the flakes are coated with a sodium hydroxide or potassium hydroxide solution and heated in a continuous mixing screw. Then, they are pre-dried in a continuous reactor and heated to a higher temperature than during the first step. Finally, the flakes are treated in a continuous rotary oven under high temperature and a dry air counterflow.
The applicant stated that “decontamination occurs by saponification/depolymerisation of a surface layer of the flakes and by diffusion of contaminants towards the surface followed by removal by air flow,” according to the publication.
But CEP said it wasn’t able to get detailed enough descriptions of all of the steps involved, it lacked information about the decontamination through depolymerization, and it questioned whether the tests conducted at lab scale were representative of industrial-scale recycling.
To receive the latest news and analysis about plastics recycling technologies, sign up now for our free monthly Plastics Recycling Update: Technology Edition e-newsletter.
More stories about Europe
- Financing, uncertainty feed EU recycler bankruptcies
- PCR mandates, global policy needed to improve rates
- European plastics recycling sector faces slew of challenges