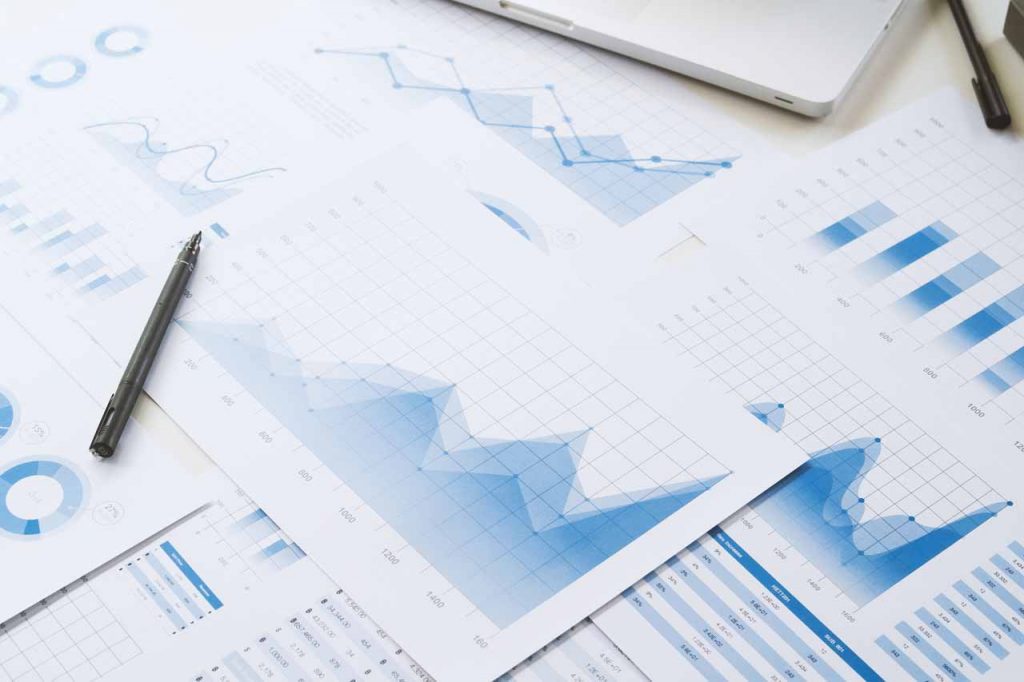
Despite challenges caused by the pandemic starting in March, the first quarter of 2020 showed strong sales for some businesses that use recycled plastic. | Chaosamran_Studio/Shutterstock
Three major recycled plastic consumers recently reported their business performance during the first few months of 2020. They touched on COVID-19, recycled material costs and their outlook for the future.
Fabric maker sees demand impact
Unifi, a Greensboro, N.C.-headquartered producer of Repreve fabric made from recycled PET, on April 30 reported its financial results for the first three months of the year.
The company recorded $171 million in net sales during that time, which is the third quarter of Unifi’s fiscal year 2020. That’s down from $180 million for the same period a year ago. Gross profits were $15.4 million, up from $13.8 million during the same quarter in 2019.
Tom Caudle, president and chief operating officer, said the first 10 weeks of the quarter were “strong and consistent” with the company’s projections. But COVID-19 altered conditions in March.
“The impacts of the pandemic on global demand began materializing at the end of the March 2020 quarter, which have placed pressure on many of our customers and the pipeline,” Caudle said.
Despite those impacts and particularly the Chinese shutdown, Unifi reported a quick and strong recovery in Asian demand. The region saw a 28% increase in sales during the quarter, with that amount led primarily by the company’s Repreve products, which are made from recycled plastic.
In a call with investors, Unifi Executive Chairperson Al Carey predicted that companies will place more importance on environmental, social and governance (ESG) initiatives as a result of the pandemic. That shift, he said, may lead to even stronger demand for the Repreve products.
Carey also noted that two Repreve projects exploring additional materials – Repreve Nylon and Repreve Ocean Plastic – have slowed in momentum during the coronavirus pandemic.
“Those two were getting tremendous interest from our customers before all this happened,” he said. “And obviously, right now, they’re focused on getting back into business, but I expect those to help us going forward.”
Flat feedstock pricing for film end user
Trex, a Winchester, Va.-headquartered producer of composite lumber products made with recycled plastic, reported its first-quarter financial results on May 4.
The company, which is a major consumer of recovered PE film, notched $200 million in sales, up 12% compared with the same period in 2019.
In the company’s earnings call, CEO Bryan Fairbanks said all Trex facilities have remained fully operational during the pandemic.
“We have been able to continue production in a safe and effective manner to meet demand for Trex products,” he said. “We are confident in our sourcing strategy and are well positioned to meet customer demand with no sourcing issues and ample safety stocks of raw material inventories, which we believe will protect us against any potential short-term supply chain disruptions.”
Fairbanks noted that Trex has seen fairly stable recycled plastic pricing, despite the fluctuating oil market and declining virgin resin prices.
“We have not really seen much of a shift on the recycled materials we’re buying,” he said, although he added that could change as the year progresses.
He said Trex also uses a small amount of virgin resin in some of its products, so the company will see some cost benefits from declining virgin prices.
Pallet producer invests in efficiencies
Greystone Logistics, a Tulsa, Okla. manufacturer of pallets made from 100% recycled HDPE, on April 14 reported $19.7 million in sales during the three months ending Feb. 29. That’s up from $17.2 million during the same period last year.
In a financial filing, the company described several recent and planned initiatives to reduce costs and increase recycling capabilities.
These include installing a new injection molding machine in March of this year, replacing an older unit; installing additional hardware and software to regulate the flow of resin and increase pallet production; adding another grinder to increase grinding capacity and reduce raw material costs by using lower-priced unground recycled plastic; and installing robotic equipment on two production lines.
Company leaders are uncertain about the economic impact from the pandemic on Greystone’s performance for the rest of the year.
“We anticipate some decrease in our production rates because of the impact to our workforce from some employees electing to stay home and declines in recruitment,” CEO Warren Kruger said in a release. Still, he said the company forecasts having a “solid quarter for sales and earnings despite the hardships” of the pandemic.
More stories about markets
- Bale pricing bucks seasonal trend, trade alliances shift
- Trex, Mohawk, Indorama report Q1 earnings
- Haulers share how weather, tariffs impacted Q1