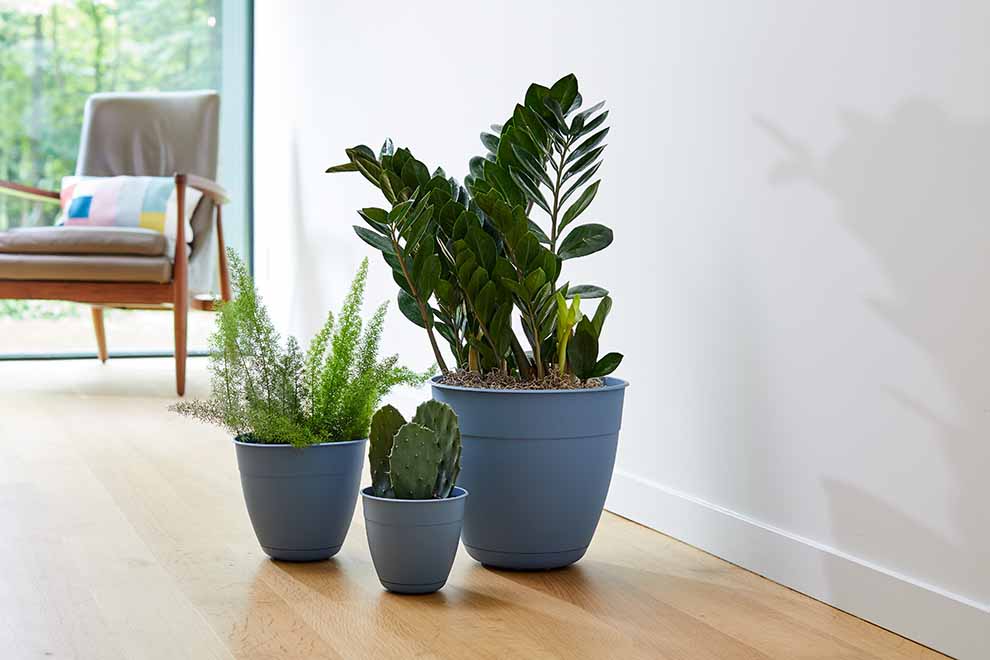
Bloem is a mid-sized planter manufacturer producing about 25 million pots a year. | Courtesy of Bloem.
A polypropylene planter producer has begun molding with marine plastics, after the company and its suppliers overcame melt flow and color consistency challenges.
Bloem on April 7 announced that Lowe’s has begun selling its Ocean Series of pots, which contain 25% marine plastics and 75% post-consumer natural PP collected through traditional recycling channels. The Ocean Series is expected to consume at least a million pounds of post-consumer plastic per year.
Based in Hudsonville, Mich., Bloem molds pots at a factory in Apopka, Fla., near Orlando. Bloem is a mid-sized planter manufacturer producing about 25 million pots a year.
Ryan Mast, company president and co-founder, said using plastic from marine sources differentiates his company in the flower pot industry, where, he acknowledged, “there’s not a ton of innovation.” Producers can change pot colors, shapes and sizes, but to truly revolutionize the industry and do something different, Bloem took up the environmental cause of recycling waste material into long-lasting products, Mast said.
But the Ocean Series didn’t come without challenges. In an interview, Mast explained how molding with the material presents difficulties and why it’s worth the effort.
Eye toward color consistency
The ocean plastics feedstock originates as discarded packaging, crates, baskets, buoys and other items on shorelines in Canada, the Dominican Republic, Haiti and Mexico, according to a press release. The plastic includes material that is both “ocean bound,” or at risk of washing into the sea, and “ocean found,” or already floating on the water, according to Bloem.
“We’d be hungry to get 100% ocean-found material at some point,” said Mast, who started the company in his home in 2012.
The plastic is baled and shipped to a reclaimer in the U.S., where it’s processed into pellets. Mast said he wasn’t able to disclose the reclaimer.
The Ocean Series is the product of three years of work. Melt flow and consistent color were among the challenges Bloem encountered. Pots are typically produced in deep-core molds, with the plastic injected from the bottom. That means a high enough melt flow is needed to form the plastic around the deeper draw, Mast said.
The marine plastics, however, have too low of a melt flow rating.
“We originally tried to work with 100% ocean plastic but the melt flow precluded us from being able to put it into our products,” Mast said. So Bloem started experimenting with mixing the ocean plastic pellets with post-consumer PP to boost the melt flow, he said.
Mixing the ocean plastic pellets with the white PP pellets is also important to achieve color consistency, which is of prime importance for Bloem’s Ocean Series pots. The series is currently available in an “ocean blue” color, ideal for marketing a product containing ocean plastics.
Courtesy of Bloem.
“Our color formulation is what really separates this material, in our viewpoint, from the rest of what’s on the market currently,” Mast added.
But achieving that color on a consistent basis was – and still is – a challenge. It took a couple of years for suppliers to dial in sorting to improve color consistency to the point where Bloem felt comfortable putting its product into the marketplace, Mast said.
Mast noted the company can’t be too picky about color because PP scrap from marine sources is limited. To narrow color variability enough so that the green pellets hit a specification Bloem could handle, ocean plastics suppliers had to collaborate to improve sorting, he said. Optical sorting was a key part of the solution.
The green pellets are mixed with white PCR and a colorant to achieve the “ocean blue” color – the company plans to roll out other colors in the future.
Despite the scrap sorting and pellet mixing efforts, color inconsistencies can occur in the finished pots. So Bloem employs a highly trained inspector who examines the pots for color consistency. When differences are discovered, the plant’s process technician adjusts the letdown ratios for the colorant, Mast explained.
“We have to have Product One and Product One Million match consistently,” he said.
Mast said much of plastic manufacturing is dialing the process in and leaving it as is, or “set it and forget it.” But the Ocean Series required Bloem staff to watch the process closely and control the variables. Some people shy away from the manual work that’s required when molding products with ocean plastics, he said.
“But when it’s more than just making a flower pot and it’s a cause of passion, I think it’s easily justifiable,” Mast said, “and I think we as a team have decided that it’s a cause we want to take up.”
To receive the latest news and analysis about plastics recycling technologies, sign up now for our free monthly Plastics Recycling Update: Technology Edition e-newsletter.
More stories about PP
- APR updates design recognition, submissions
- Denton Plastics building major Oregon PP expansion
- Missouri MRF upgrades PP recycling capabilities