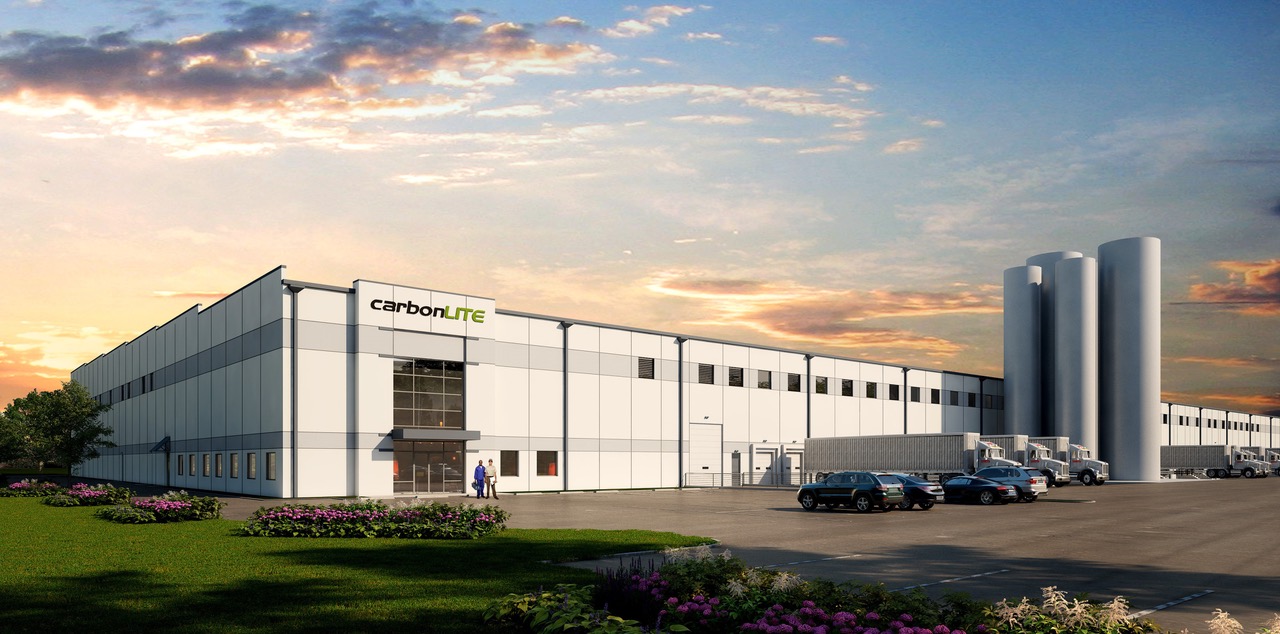
CarbonLite’s Reading, Pa. plant will produce recycled PET for use in water bottles, thermoforms and other products. | Rendering courtesy of CarbonLite
PET processor CarbonLite is nearing the opening of its third facility, which will produce 85 million pounds of post-consumer resin per year.
The company, which operates processing plants in Riverside, Calif. and Dallas, first announced a new facility in Pennsylvania in spring 2018. Since then, both the investment figure and planned capacity have increased.
The facility was driven primarily by two of CarbonLite’s major customers, Nestlé Waters North America – which signed a pre-buy agreement to source pellets from CarbonLite – and Niagara Bottling. These companies use significant amounts of recycled plastic in their bottles, and both have bottling plants in Allentown, Pa.
CarbonLite’s new facility is located in Reading, Pa., about 20 minutes from Allentown. In all, the company plans to invest $80 million in the plant, up from an initial estimate of about $60 million. The company’s Riverside and Dallas plants carried investments of $60 million and $62 million, respectively.
The company placed orders for processing equipment about a year ago, and it is slated to arrive and begin the commissioning period in the coming weeks.
“We are planning to be in production by the first quarter of 2020,” said Leon Farahnik, CEO of CarbonLite, in an interview.
The Pennsylvania plant comes at a time when numerous brand owners are making recycled plastic commitments, but the CarbonLite plant was in motion before the latest groundswell of brand owner goals.
“When we decided on going forward with Pennsylvania a year ago, it wasn’t that much of a factor at the time,” Farahnik said. “It just showed that the Nestlés of the world and the Niagras of the world, they foresee what is happening and foresee the need for the post-consumer content.”
Producing 85 million pounds of pellet annually
The plant will total 270,000 square feet, which is larger than the company’s other facilities. Farahnik said the bigger size will allow CarbonLite to store more bales inside and have a higher production rate.
The facility is being outfitted with a sorting system with optical and robotic equipment from Bulk Handling Systems, a wash line from Sorema, a flake sorting system from Van Dyk/Tomra, solid state polycondensation (SSP) equipment for food-grade pellet production from Starlinger, and more. The wash line will be able to process about 20,000 pounds per hour.
Like CarbonLite’s existing facilities, the Pennsylvania plant will process all plastics into pellets and will not sell any flake. Some of the facility’s output will go to thermoform applications, but 90% of the pellets will be used by beverage companies. Farahnik projected the facility will produce 85 million pounds of food-grade pellets per year.
The Northeast is an attractive region for sourcing bottles because of the concentration of container deposit states. Pennsylvania, itself, has no container deposit system, but Farahnik noted that’s not the only indicator of available bottles.
“We don’t have a deposit system in Dallas either and we get ample supply for our Dallas facility,” he said. “We feel there is enough availability of bales in the deposit states and the surrounding areas for us to be able to run our facility.”
Bale yield decreases
CarbonLite only processes post-consumer PET bottles. To produce those 85 million pounds of pellets, the company will need to source significantly more due to yield loss. That’s always been the case, but Farahnik has seen an increase in yield loss in the past two years.
“The truth is, the quality of bales has deteriorated since the China issue,” he said, referencing the National Sword import restrictions China implemented at the start of 2018. “It definitely has. It’s a fact.”
Although it’s difficult to prove the cause, one contributing factor could be bale suppliers including more non-conforming bottles in PET bales as a way to move material with weak markets.
Whatever the cause, CarbonLite has calculated how much weight it can expect to lose during processing.
“You have to figure that you lose about 30% in deposit states with deposit bottles and about 40% when it is from curbside,” Farahnik said.
To receive the latest news and analysis about plastics recycling technologies, sign up now for our free monthly Plastics Recycling Update: Technology Edition e-newsletter.
More stories about PET
- APR updates design recognition, submissions
- Plastics treaty talks end without consensus or a plan
- Republic Services sites third polymer center in PA