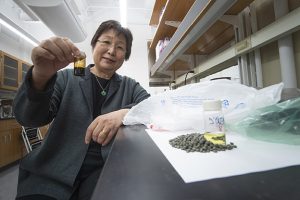
Purdue University professor Linda Wang shows the oil product from a new polyolefin-to-oil conversion process.
A team at Purdue University has developed a unique method for converting scrap polyolefins into oil, fuels or monomers for use in new plastics.
The conversion process uses selective extraction and hydrothermal liquefaction to convert plastic into naptha, which can be used to create other chemical products, according to a press release.
“The polymers will … melt in the high temperature and dissolve in the supercritical water, and then in this state they can convert into oil, or monomers or gas,” Linda Wang, a chemical engineering professor and leader of the research team, stated in a video. “It’s a very versatile, powerful technique.”
Some results of Wang’s research were published in January by the American Chemical Society (ACS) in its Sustainable Chemistry and Engineering journal. In addition to Wang, the other inventors of the technology and authors of the paper were graduate student Kai Jin and postdoctoral researcher Wan-Ting Chen.
According to their paper, PP scrap was put into supercritical water (water that’s under high temperature and pressure and isn’t in a distinct liquid or gas state). Up to 91 percent of the plastic was converted to oil when placed in supercritical water at 450 degrees celsius for between 30 minutes and an hour. The resulting product consists of olefins, paraffins, cyclics and aromatics. About 80-90 percent of the components had the same boiling point range as naphtha oil, a feedstock for multiple chemical products, according to the paper.
“Preliminary analyses indicate that this conversion process is net-energy positive and potentially has a higher energy efficiency and lower greenhouse gas emissions than incineration and mechanical recycling,” according to the paper. “The oil derived from PP has the potential to be used as gasoline blendstocks or feedstocks for other chemicals.”
The team is collaborating with others at Purdue University to optimize the conversion process for producing high-quality gasoline or diesel. They’re looking for investors or partners to help demonstrate the technology at commercial scale. The technology is patented through the university, which is located in West Lafayette, Ind.
Photo credit: Purdue Research Foundation image/Vincent Walter
To receive the latest news and analysis about plastics recycling technologies, sign up now for our free monthly Plastics Recycling Update: Technology Edition e-newsletter.
More stories about technology
- RIT researchers develop AI-based textile recycling system
- Industry nuance is key in adopting emerging technology
- Google, Dow partner on AI to identify recyclables