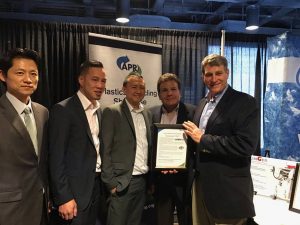
APR’s John Standish (far right) with the team that created the Lush Black Pot cosmetic market product.
Advances in plastics recycling equipment and chemistry – and a couple of recycled content products – took the spotlight at the second-annual Plastics Recycling Showcase.
Organized by the Association of Plastic Recyclers (APR), the showcase was held in conjunction with the Plastics Recycling 2017 conference in New Orleans. Innovations chosen for the 2017 showcase were announced during the APR Technical Forum on March 6. Representatives from the companies showed off their products in the exhibit hall.
The program’s goal is to highlight and commend industry-leading innovations from APR member companies that support the growth of plastics recycling, according to APR.
“This is the second year of the APR Recycling Showcase Program, and we had a great deal more submissions this year,” said John Standish, APR’s technical director. “We see the Showcase becoming a widely anticipated part of the conference program in the years ahead and hope that by APR identifying and recognizing innovations that positively impact plastics recycling more companies will be encouraged to participate in the future.”
Following are summaries of the products chosen for the 2017 showcase. To see Plastics Recycling Update’s coverage of the 2016 showcase, click here.
De-labeling technology
Italian plastics equipment company Amut Group was featured for its de-labeler, which removes labels from PET bottles while minimizing damage.
The Novara, Italy-headquartered company makes three models of de-labeler, with capacities of 3,300 pounds per hour, 6,600 pounds per hour and 13,200 pounds per hour.
“The AMUT De-Labeler is a continuous dry pre-cleaning system removing both standard wrap-around and full-body shrink sleeve labels from PET bottles ahead of the wash line,” according to a product innovation description. “After label removal, the bottles have good integrity without damage.”
The two larger-capacity models are currently operating in North America. Last fall, Plastics Recycling Update highlighted the use of the dry de-labeling equipment at a new Unifi plant in Reidsville, N.C.
Amut Group has four divisions making equipment for extrusion, thermoforming, recycling and printing/converting.
Recycling-friendly labels
Glendale, Calif.-based Avery Dennison has created a recycling-friendly paper label for thermoforms. It’s the only paper thermoform label to meet APR’s benchmark criteria, according to a product description states.
The company’s CleanFlake portfolio of pressure-sensitive labels originally launched in 2012 to advance the recycling of PET containers. Labels in the line feature a water-based recyclable adhesive. It adheres to the PET bottle or thermoform until the float-sink tank process, where it separates from the plastic.
“This allows the facestock and adhesive to cleanly separate from the PET flake, resulting in pure PET flakes, the conservation of virgin PET resources and less landfill waste,” according to a product description.
Last year, Avery Dennison introduced an improved adhesive that works for either film or paper labels on thermoforms.
Tube for lotions
Evansville, Ind.-based Berry Plastics was recognized for creating squeeze tubes with up to 62 percent post-consumer recycled HDPE. Most tubes on the market container no post-consumer resin.
The company made a series of squeezable tubes holding lotions for dogs. The lotions are from a company called “Fetch … for Pets!,” which bought a license to market the products under the Burt’s Bees Natural Pet Care name.
Depending on the size of tube, they will contain from 57 percent to 62 percent recycled plastic (excluding the closure). The tube shoulder, which is the stiff end where the body connects to the closure, contains a higher percentage of recycled content than the squeezable body.
“We found this PCR amount allows the tube to meet all the same quality, performance, and processing standards as non-PCR tubes,” according to a showcase innovation description.
Berry Plastics Group is a publicly traded company specializing in value-added plastic consumer packaging, nonwoven specialty materials and engineered materials.
Compatibilizer advancement
The Dow Chemical Co. received recognition for its Retain polymer modifiers, which are compatibilizers that allow converters to recycle barrier film trim back into film production without sacrificing optical or physical properties.
“Compared to other control films, Retain Polymer Modifiers help make packages clearer, maintain mechanical properties, and significantly reduce gels in films produced from barrier film recycle streams,” according to a product description.
The Retain polymer modifiers are also being incorporated into Dow’s RecycleReady Technology packaging. Retain is being used as an embedded compatibilizer in multi-material packaging, allowing it to be recycled via traditional retail PE film collection channels.
“Packaging made with this technology can be recycled back into a polyethylene recycling stream, addressing current recycling challenges and complications in multilayer flexible barrier packaging due to differences in material properties,” according to a product description.
Plastics Recycling Update featured the technology last summer.
Headquartered in Midland, Mich., Dow is a global supplier of every major PE family worldwide.
New melt filtration approach
Germany-based company Ettlinger drew attention for its developments in melt filtration technology.
The company’s ERF and Eco filters use ridged cylindrical filters that rotate and are continuously wiped clean of contaminants. With the new technology, frequent screen changes and backflushings aren’t needed, which means improved pressure stability and equipment up times.
The latest series of Eco filters makes possible the cleaning of low-viscosity plastics, such as PET and nylon.
Ettlinger says the technology offers several advantages over back flush or filter wheel screen changers. For example, their continuous, self-cleaning operations allows them to operate for weeks or months with stable operating pressures, according to a product description. The system can maintain consistent pressure, even when cleaning highly contaminated streams, by adjusting the speed of rotation.
The ridged screens have conical holes, eliminating mesh expansion and preventing gels and cross-linked materials from passing by the filter.
In addition to melt filters, the Königsbrunn, Germany-headquartered company specializes in developing and building injection molding machines.
Cosmetics container
Troy, Ala.-based KW Plastics was highlighted for developing the first post-consumer PP resin greenlighted for cosmetic product packaging.
KW Plastics developed a 100 percent recycled content resin that’s molded into containers for Lush Fresh Handmade Cosmetics, a 22-year-old company that emphasizes reducing environmental impact. The recycled plastics received letters of no-objection from the U.S Food and Drug Administration.
The Lush Black Pot, as the container is called, includes an injection-molded container and lid made to hold cream and lotion. KW Plastics supplies the recycled resins to Plascon Plastics.
KW Plastics says it’s the world’s largest plastics recycler and post-consumer resin supplier for HDPE and PP. It can process more than 650 million pounds a year.