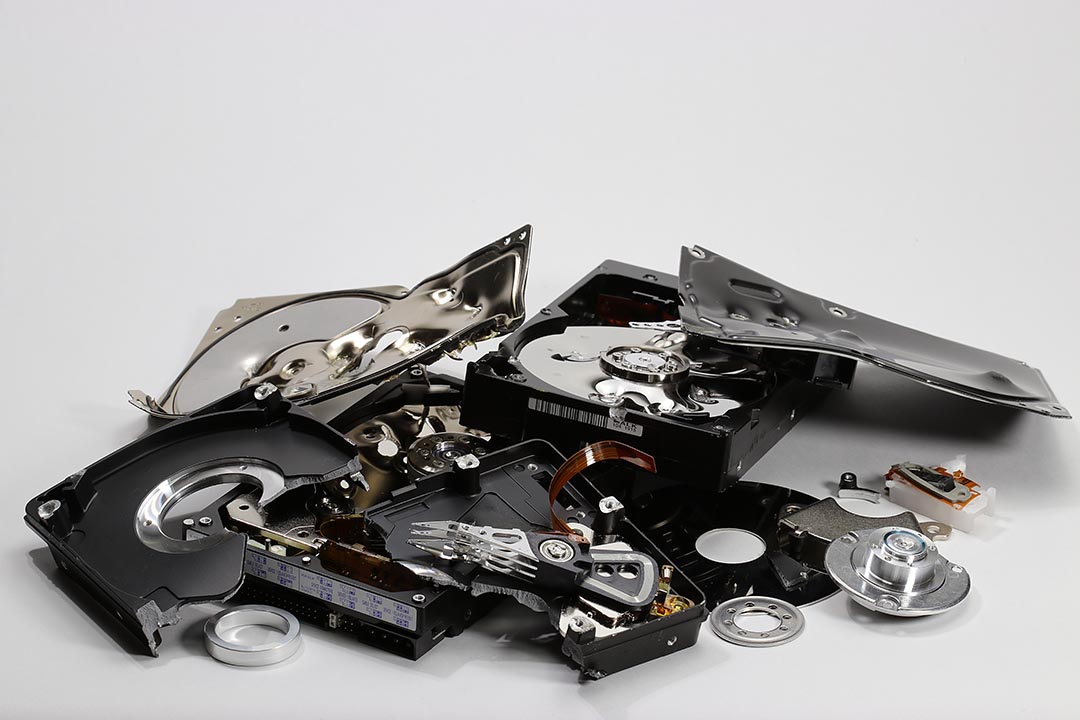
Hard drives provide one source of rare earth elements in the end-of-life electronics stream. | Kazu326/Shutterstock
As rare earth elements draw mainstream headlines for their entanglement in the U.S.-China trade war, recent announcements from an ITAD operator, an OEM and a magnet processor indicate the domestic end-of-life device stream is increasingly providing feedstock for rare earth end users.
Rare earths are used in several applications in consumer electronics and IT equipment, and China is by far the world’s largest supplier of the minerals. The Chinese government recently further restricted exports of rare earths as part of its response to U.S. tariffs on Chinese goods.
The supply chain disruption is projected to affect U.S. manufacturing in a number of ways. Tesla, for instance, this week announced the magnet supply challenges will likely delay its plans to build humanoid robots.
Supporting domestic sources of rare earth minerals has become one priority for President Donald Trump’s administration – last week, he issued an executive order that, among other points, called for U.S. government support of critical mineral recycling efforts, including rare earth recovery.
Additionally, rare earths have played heavily into negotiations between the U.S. and Ukraine, with the U.S. seeking to secure rare earths from Ukraine in exchange for aid.
Amid the rising attention on this relatively low-profile material stream, several projects recovering rare earths from electronics recently announced expansions.
Chemistry advancements and data center angle further recovery
ITAD firm Illumynt has been recovering rare earth magnets from hard drives for some clients for about five years. This month, Illumynt announced it is expanding this part of its business, driven largely by its development of what Mike Hammond, a senior vice president at Illumynt, described as a “very sophisticated process for doing it at scale.” He noted rare earth recovery provides a “modest net positive,” although it’s not a big moneymaker.
The company developed equipment that can either be used in an ITAD facility or on-site in a data center. The equipment mechanically separates the small portion of the drive that contains the rare earth magnet from the larger portion of the drive, which consists of the platter and circuit board.
Illumynt then uses a proprietary chemical concoction that changes the rare earth magnet into powder form, from which the minerals can be recovered by a downstream processor. The company’s downstream customers have varied but include companies in the supply chain for major OEMs producing hard drives.
Paul Knight, CEO of Illumynt, added that recovering rare earths from end-of-life devices has become much more feasible in recent years due to scientific and technological advancements.
“Ten years ago, it would be crazy to try to do it,” he said. But advancements in the chemical solutions to produce powdered rare earth fractions is a “dealbreaker,” he said. Additionally, the growing presence of ITAD operators in the data center space has enabled this type of recovery: Processors are in the door and have access to large consistent quantities of hard drives.
An April 17 announcement from Microsoft, PedalPoint Recycling and hard drive producer Western Digital similarly highlighted how data center decommissioning and newly developed chemistries are enabling rare earth recovery.
The companies recently completed a pilot project that used an “acid-free dissolution recycling” technology to recover rare earths from about 50,000 pounds of shredded Microsoft data center hard drives and related assets. Their process was able to recover roughly 90% recovery of rare earth elements from the materials.
“When scaled worldwide, this new recycling process could return a lot of recovered rare earths to the U.S. supply pool,” the companies wrote.
The chemical process also recovered gold, copper, aluminum and steel, they wrote. In all, the “advanced chemical processes” and “meticulous segregation of components” enabled recovery of 80% of the mass of the inbound materials.
Magnet recycling company enters US
Canada-headquartered Cyclic Materials this week announced it will site its first U.S. facility in Mesa, Arizona, where it will recover magnets from hard drives, electric vehicles and more.
The company went through research and development at its initial location in Kingston, Ontario, where it experimented with hard disks and other materials streams. It ultimately developed a proprietary magnet removal process and has been looking to scale it up with its first commercial facility.
Cyclic Materials’ upcoming facility in Mesa, Arizona. | Photo courtesy Cyclic Materials
On April 23, the company announced that location will be a 150,000-square-foot facility in Mesa, Arizona, slated to start up in 2026.
Kunal Phalpher, Cyclic Materials’ senior vice president of corporate development, told E-Scrap News the facility was in development well before the recent wider attention on rare earths. But he agreed the growing emphasis on enhancing domestic rare earth supply, and similar focus on nearshoring critical minerals supply chains in both the U.S. and Europe, stand to benefit the recycling sector.
“These are just tailwinds for us to continue to acquire feedstock and build out capacity to bring those materials back into the supply chain,” Phalpher said. The recycling sector, he added, has an advantage of being able to set up and scale up facilities faster than mining companies or others engaged in the primary materials sector.
The Mesa facility will have a projected capacity to process about 55 million pounds of end-of-life components per year. Phalpher estimated hard drives could make up less than 10% of the total weight processed at the location, however, given their size compared with feedstock items like electric vehicle motors.
Cyclic will be a downstream for ITAD and e-scrap companies that recover drives. The company’s process, dubbed MagCycle, separates hard drives into their metal components, including copper, aluminum, steel and the magnet, which typically contains elements such as dysprosium, neodymium, praseodymium or terbium. The metal components are sold to metals buyers.
For the extracted magnet, Cyclic also developed its own hydrometallurgical refining process, titled REEPure, that processes magnets into a mixed rare earth oxide, a cobalt-nickel hydroxide and other mineral streams. Then, the company has formed supply partnerships with downstream processors who further refine the mixed rare earth oxide, pulling out the individual rare earth elements.
One such agreement is with Solvay, a chemical company that recently started a French production line producing magnet-ready rare earths for magnet manufacturers. Another is with Vacuumschmelze, a German magnet producer that is in the process of setting up a magnet production facility in South Carolina with support from the U.S. Department of Defense.
Beyond hard drive magnets, in the consumer electronics stream Cyclic is exploring recovering rare earths from other portions of devices. Earbuds often contain magnets, and cell phones rely on neodymium and dysprosium to perform their vibrating function. The challenge in tackling new areas is in the economics, Phalpher said.
“If you’re going to buy earbuds and get 80% plastic, is it going to work out economically in our process?” he explained. “Whereas we know hard drives have that potential.”