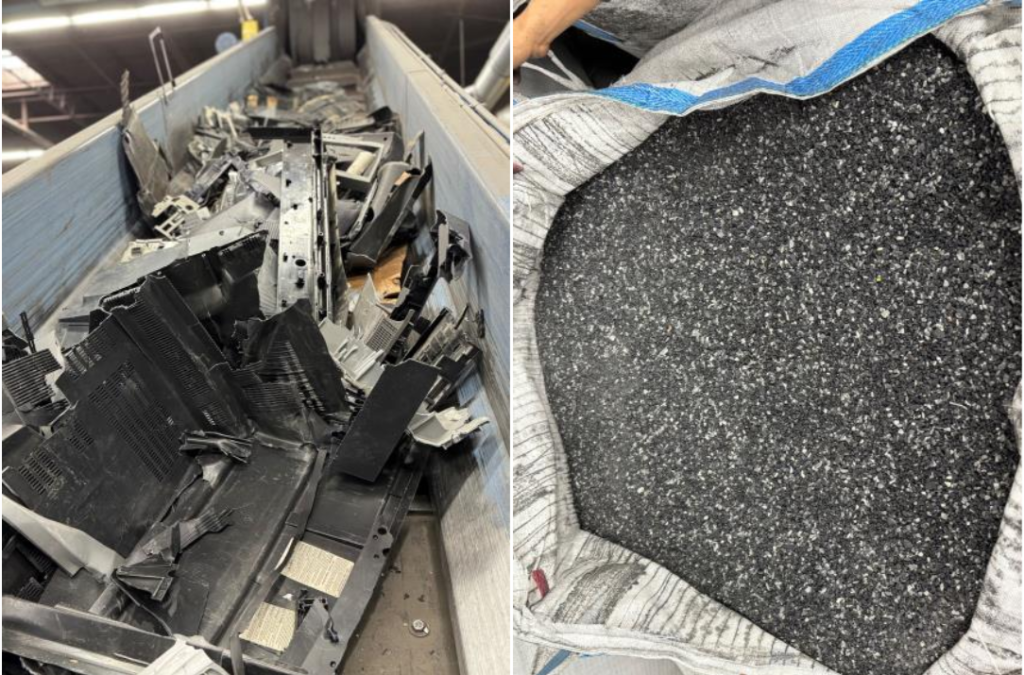
Com2 is shredding and sorting e-plastics at its Carol Stream plant in Illinois. | Photo courtesy Com2 Recycling Solutions
North American e-scrap processor Com2 began processing e-plastics in-house at the beginning of the year after global regulations on material movement challenged longstanding export pathways.
Com2 Recycling Solutions, which operates a facility in the Chicago area and another in Mississauga, Ontario, is a longtime processor well-known for processing CRT glass into a feedstock for tile frit, an ingredient in compounding enamels and ceramic glazes. In recent months, the company’s U.S. facility has invested about $1.4 million to install new equipment to process a range of plastics commonly found in electronics.
“We generate a lot of plastic, because of CRT processing and flat-panel processing,” said Saheem Baloch, CEO of Com2, in an interview with E-Scrap News. Com2 generates 600,000 to 900,000 pounds of e-plastics per month, Baloch estimated, or about 7 million to 11 million pounds per year. Most of the plastic the company generates is ABS and polycarbonate, commonly used in TVs and flat-panel displays as well as printers and keyboards.
In the past, “it was easy to sell the plastic, because a lot of buyers were buying and selling to Malaysia,” Baloch said.
But the e-plastics landscape has shifted substantially in recent years, driven by changes to the Basel Convention, the global treaty regulating shipments of end-of-life materials. A plastics-focused amendment that took effect in 2021 changed the requirements for many countries, including common U.S. export markets, to import scrap plastics. And beginning in January of this year, an e-scrap-focused amendment added new requirements for shipping end-of-life electronics around the globe.
The 2021 plastic amendment did not cause an immediate end to e-plastic exports – by late 2023, industry watchdog the Basel Action Network issued a warning that numerous domestic processors were still exporting plastics in violation of the Basel Convention, which the U.S. isn’t a party to but which the e-Stewards and R2 e-scrap certification standards expect certified companies to adhere to.
The major obstacle to compliance has been lagging domestic e-plastics processing capacity. Some companies have taken advantage of the emerging business opportunity, and Com2 is among the recent entrants in this space. Com2 knew the Basel regulations were increasing scrutiny on mixed-material exports, Baloch said, and the company knew one solution was to increase its in-house sortation abilities to both move materials and maintain its R2 compliance.
The company this year started up a full shredding line capable of processing 2 million pounds per month, or 24 million pounds per year. Baloch explained the line takes the plastics through two shredders and a series of hammer mills, granulators, magnets, washing tanks, dryers and sorting tanks. At the back end, the material comes out in ABS or PC regrind fractions. Baloch said the company has tested the ABS stream and found it to achieve 98% polymer purity.
Com2 is also planning to install additional sortation equipment, including electrostatic separation equipment to separate any PS out of the ABS stream and equipment to provide greater sortation by color. But even without full color sortation, shredded regrind consisting almost exclusively of one polymer is enough to get the plastic out of the scope of Basel control, according to R2.
The company isn’t pelletizing the e-plastics in-house, but it’s evaluating whether the market exists to add pellet production capacity.
“At this moment, our customers are asking for regrind,” Baloch said, particularly because the customers are typically compounders who will mix the regrind with other feedstock, such as virgin plastic, to meet certain criteria before pelletizing.
Most of those customers are North American buyers, he said.
Com2’s Canada facility now sends its e-plastics to the Illinois facility for processing. Other e-scrap processors are doing the same, because the company’s processing capacity is more than double its typical in-house generation.
He added that the company is bringing in full plastic-heavy devices from other processors as well as plastic components that have already been removed from devices. Com2 prefers to receive whole devices rather than shredded fractions because it’s easier to separate components from the whole device in preparation for e-plastics processing, rather than isolating plastics from a shred mixture that includes lots of other contaminants, but the company does accept both.