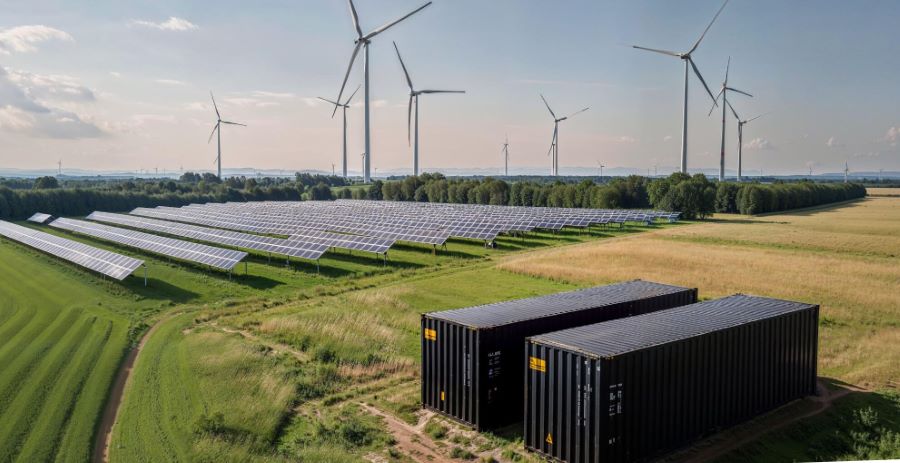
Germany’s Kraftblock develops storage systems to capture waste heat from heat-intensive processes including e-scrap recycling. | Courtesy of Kraftblock
Despite its value in the sustainability sphere, recycling e-scrap is heat- and energy-intensive. Germany-headquartered Kraftblock says the electronics recycling industry needs physical solutions to decarbonize its heat and energy use.
While several methods of harvesting e-scrap exist, they all require extremely high heat. For example, the pyrometallurgy process maintains temperatures of around 750 to 1,500 degrees Fahrenheit, and lead smelting can be almost as hot, according to Kraftblock, a firm specializing in energy storage.
E-scrap is the fastest-growing type of discarded material globally, per the World Economic Forum, owing to rapidly changing technology and consumer preferences that make electronics seem disposable. The heat generated by recycling processes also typically emits large amounts of carbon dioxide and other greenhouse gases that can be avoided – including with power generated via captured heat.
Kraftblock’s power-to-heat thermal storage system converts renewable electricity into heat with minimal disruption to existing infrastructure, CEO Martin Schichtel said in a recent interview with E-Scrap News. Kraftblock customizes its technology to provide large-scale, long-duration energy storage, supplying hot air, thermal oil, steam or water at temperatures of up to 2,400 degrees.
The following Q&A has been edited for clarity and brevity.
What issues does Kraftblock seek to address with your systems?
Our big goal is to cut down on emissions, to decarbonize various heat-intensive industries. So for that reason, we developed a common energy storage platform. In the middle you have a kind of storage which will collect heat connected to various charging and discharging options, and so you can decarbonize, or at least cut down on emissions, via heat processes. It could be waste heat recovered – steel, glass, ceramic produce a lot of waste heat. You can recover it and put it in the storage device, and then discharge to whatever process you need, to directly reduce the emissions in those processes.
It’s hard to picture capturing and storing heat, so is there a layperson-friendly way to describe the process?
At the moment, I’m on holiday, and so the simplest analogy is to use the sand at the beach. During the day, it’s getting incredibly hot so that you have to use your shoes, right? And that’s the same principle that we use, in a more technical way. Our storage device absorbs the heat. It discharges the heat to this colder environment. We use up to 85% of recycled materials in our storage systems – for example, upcycled steel slag and inorganic waste. So we combine technological benefits with the circular economy.
Why did we select, for example, steel slag – it’s getting generated by the megaton every year for 60-70 years. It’s available worldwide. So there is no issue with the supply chain. It’s a mixture of looking where materials are available and looking to where storage and power is needed, because what we do not want to do is to produce material in Germany and then ship to Australia for an application.
What is the process of establishing a storage system, starting from when a potential customer first considers implementing it?
So usually first we are asking the customer, what is your process? What is the energy generation? What is the energy generation in the system? What is your goal with this project?
We also ask: What are your thoughts about using such a system? What would you like to improve – is it the footprint, is it a specific temperature? Then when we get the green light, we start a feasibility study by digging more into the details, and how can we integrate it in a very small spot in time so that the production is not standing still for a couple of weeks.
What are the benefits to a client of installing such a system?
I think next month, or a month later, we will publish a project with one of the largest steel manufacturers in the world where we install a waste heat recovery system. And this waste heat recovery system reduces gas consumption, reduces another 20,000 tons of carbon dioxide, which is a brilliant effect already. It also increases the efficiency in such a plant, which means each ton that’s getting produced has a lower carbon dioxide footprint, has a better energy efficiency, and the whole sector will be strengthened as well.
That’s the beauty of this storage system, you can always use electricity to the maximum, cheapest price of the market. You even improve the safety on site, because if you do not have to handle gas, there’s nothing which can explode. Also in terms of insulation, it’s that well-insulated that it never gets hotter than 50 degrees Celsius on the outer shell, which is much lower than typical process you see in those industries.
You can also distribute excess energy generated from the recovered waste heat, out into the grid?
Yes, yes, you have multiple functions – you can use the heat for process. If you talk about waste recovery, you can use heat for the same process. If you talk electrification, it’s exactly the same. But you can also decide to deliver heat to another process: could be a district heating system, could be the third-party customer outside your own plant. Because if we think about plastics recycling or about rubber tires, or pyrolizers, they have enough heat so they can use the power and they can sell the rest of the waste heat to another company from the same location, be it a strategic system, could be a utility, so you can use the heat multiple times.
But that could also be done, for example, for e-waste recycling. So they have high temperatures, 1,200 degrees Celsius, sometimes even higher, which means they do have waste heat at that temperature potential. You harvest that waste heat, then put it into your storage device.
So would you say that most of the systems are custom, or are there a lot of similarities between companies and industries?
Storage is always the same. The infrastructure for charges and discharges is a bit different, but most of the parts, again, are the same. So we de-risk the product that way for the customer and standardize it with each application. Our storage is based on 20-foot storage containers, the same for liquid. If we need higher storage capacity, then we put two, four, 10, 20 of those containers to go to larger storage capacity. So it is a bit tailored.
What would be a typical time frame from start to finish?
On average, from the very first analysis of the data till the installation usually the time frame is between six months for a small system and 12-18 months for a large system. It depends a little bit on the location. It depends on the time it takes to file building permits, to get that storage integrated into the existing site. There are a couple of regulations we have to check as well, and usually, in our experience, filing permits takes more time than building the whole system itself. If everything is on stock in our location, storage can be built within three months and delivered in three months. For most of the components there are multiple suppliers in the market.