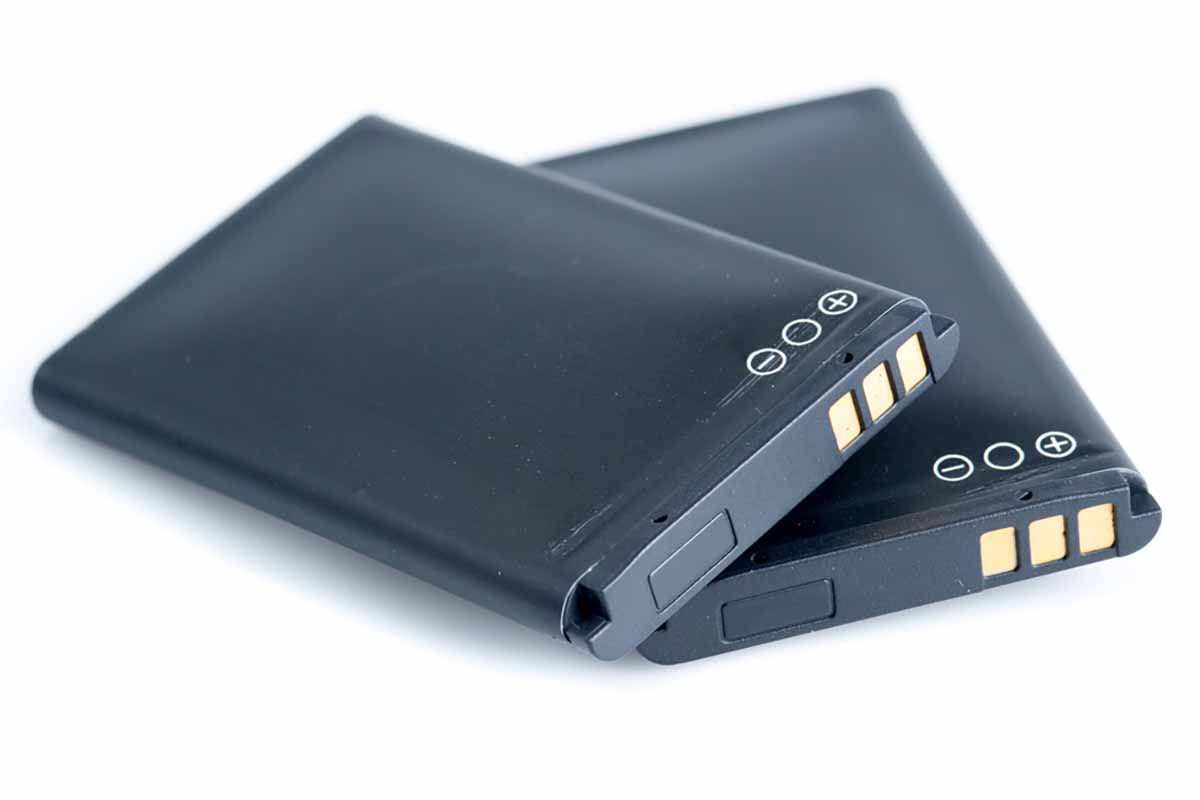
Lead battery recycler Ecobat is moving into lithium-ion battery recycling with three facilities, two in Europe and one in the U.S. | Showcake/Shutterstock
Lead battery recycler Ecobat’s first U.S. facility for recycling lithium batteries is being commissioned, and the company is already looking at what comes next.
Dallas, Texas-headquartered Ecobat has 11 smelters across two continents and an average annual output of 840,000 metric tons of lead. Its lead recycling recovers and repurposes over 99% of the metal input, a press release noted. It also recycles some polypropylene at select facilities.
Elliott Ethridge, vice president of global sales for Ecobat, told E-Scrap News that Ecobat “has a really proud and long history in lead recycling that goes back decades and spans multiple continents.”
“It makes sense to go now into lithium,” he said. “We see a very good space for moving forward. We don’t see lead diminishing – it’s not a zero sum game. We see lithium coming on to augment a lot of spaces that lead doesn’t serve.”
Ecobat is the only European provider of fully integrated Stage 1-3 lithium battery recycling services, the press release noted.
Ethridge said that Ecobat leveraged its long experience with handling lead batteries to leap into the lithium-ion battery market. After doing research, the company decided to forgo pilot plants and start building full facilities.
One, in Germany, is already online. Another in Casa Grande, Ariz. is “being commissioned as we speak,” Ethridge said. The third facility, in the U.K., will come online soon, he added.
The Arizona facility has a capacity of 10,000 tons of recycled material per year, with the ability to expand capacity. It will sort, shred and separate battery materials to produce black mass.
Ethridge noted that black mass end markets are currently diverse and spread out all over the world. Ecobat wants “to make sure the markets function the best way they can,” he said, as it’s a “global topic that has regional ramifications.”
“We have expansion plans from there that I cannot share, but we very much intend to maximize the facilities and learn as much as we can and partner with the right people and then grow,” Ethridge said.
As for feedstock, Ecobat’s technology can handle a wide range of form factors and is chemistry agnostic, allowing the facilities to accept everything from portable small format batteries such as tool batteries, laptop batteries and cell phone batteries, to large formats such as EV batteries.
The company also looks to recover “any scrap, byproduct, off-spec, end-of-life and damaged product along the way,” Ethridge added.
Lithium-ion batteries have garnered much attention lately as the cause of fires. Ethridge said those working in the metals space have “always been hyper aware of the need for safety and the need for treating these very beneficial materials the right way.”
Lead, for example, can be hazardous to human health and the environment if not managed properly, but it, just like lithium-ion batteries, is “not inherently dangerous,” he said, it “just calls for education.”
As lithium-ion batteries enter the consumer market in a wide range of formats and applications, that makes collection and recycling “a lot more nuanced and a lot more front-of-mind for people who have not experienced these things before,” Ethridge said.
Recyclers, as stewards of the industry, can help educate consumers, he added.
“I think of our women and men in the field who go out and pick up these batteries as the first line,” Ethridge said.
Looking to the future, Ethridge predicted ebb and flow for lithium-ion recycling.
“There’s going to be a lot of excitement and then some tamping down, and then more excitement and more tamping down, but overall the trend is very positive for consumers and the environment and the recycling market,” he said.