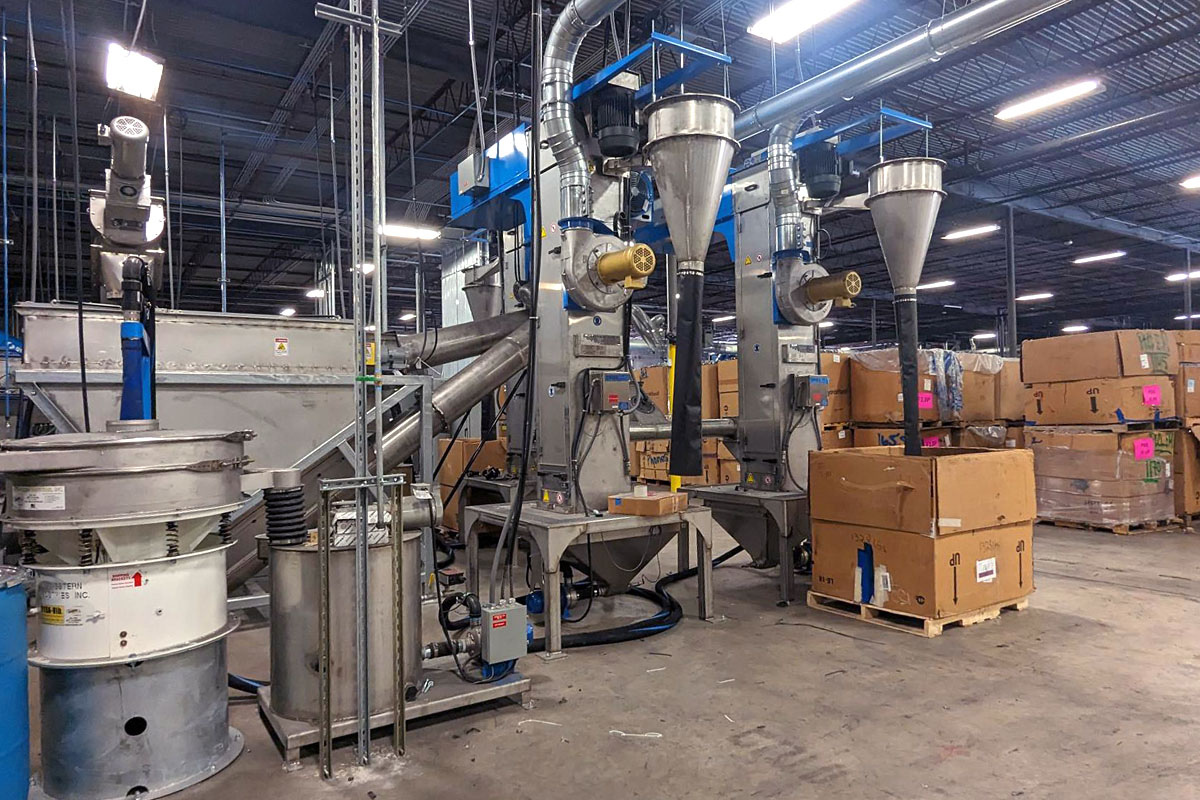
Leaders at CompuCycle say the recently installed e-plastics line will help the company sell to the domestic market. | Courtesy of CompuCycle
Houston-based processor CompuCycle is putting the finishing touches on an e-plastics sorting line, the latest domestic investment in plastics processing capacity.
“Our goal has always been to produce clean PS, ABS, PE, PP plastics to recycle for domestic reuse, and putting this plant in place is going to allow us to achieve that,” said Clive Hess, executive vice president of CompuCycle.
The sorting line, which includes a float-sink system, has been installed at a processing facility in Houston. The facility was expanded from 40,000 square feet to 50,000 square feet to accommodate the new system and its materials storage requirements.
Shredded plastics coming off the end of the e-scrap shredding and separation system are fed into the plastics line, which separates metals for recovery and sorts plastics based on their density (different polymers, as well as filled and fire-retardant polymers, have different densities). The company installed its shredding and separation system about five years ago.
The line came in with assistance from Jim Cornwell, who was a founder and longtime owner of Universal Recycling Technologies (URT), which has installed e-plastics sorting systems at its plants across the country. Now semi-retired, Cornwell, who said he has known Hess for decades, picks and chooses the projects he works on, although this is now the “biggest iron in my fire.”
Providing another alternative to SE Asia
The line was installed in the building that houses its shredding and separation system. That building is just a short walk away from the company’s 80,000-square-foot refurbishment and demanufacturing plant, both in northwest Houston.
CompuCycle started receiving equipment for the plastics line about three months ago. In late August, Hess said the system was undergoing plumbing work and would be operational in September.
Hess described the project as “a multimillion-dollar investment.”
Cornwell said the inputs will total roughly 3 to 4 tons per hour. The float-sink system separates polyolefins such as polyethylene and polypropylene, which float, from the styrene plastics ABS and polystyrene, which sink. The output will include a clean metals fraction for sale to smelters, a pure ABS/PS mix that will be sold to domestic markets, a PE/PP fraction that will be sold domestically, and waste plastics, which consist of a hodge-podge of mixed polymers.
Hess estimated the system would produce 48,000 pounds of shredded, washed plastic on one shift.
He and Cornwell said the system will allow CompuCycle to sell into domestic markets. Hess noted that it would alleviate environmental concerns from many of the company’s suppliers about how the plastic is processed.
At the same time, changes to the Basel Convention, a global treaty that covers exports and imports of hazardous waste, have obliged many governments to impose additional restrictions on the international trade of lower-grade recovered plastics.
He foresees the window for shipping mixed plastic to Malaysia, where a lot of U.S. e-plastics have been sent, “closing quite quickly.”
“We’re looking at a solution moving forward, where there are markets, and Malaysia is not a good long-term market,” Hess said.
A version of this story appeared in Plastics Recycling Update on Sept. 26.