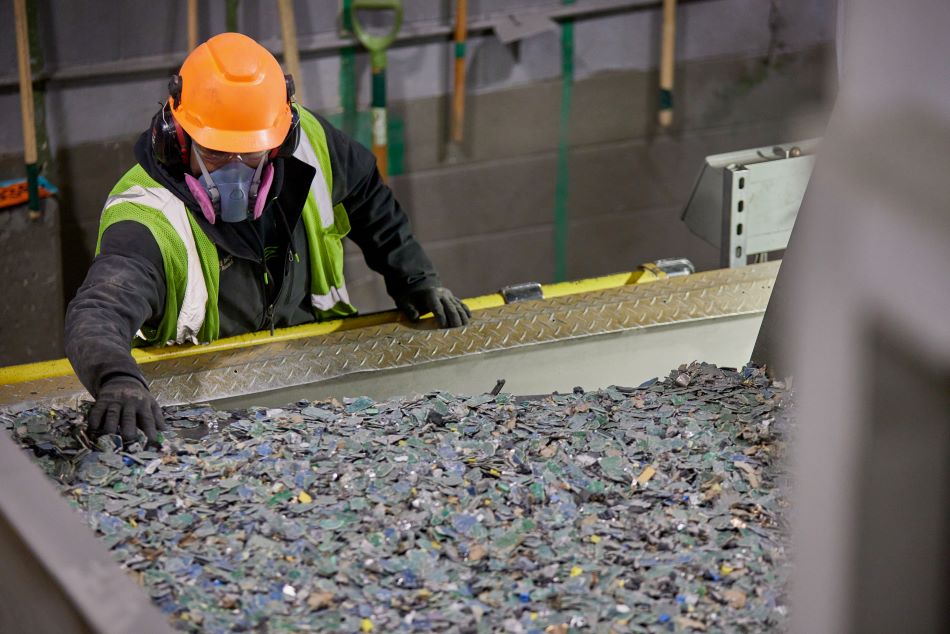
A worker inspects shredded material at a Glencore sampling facility in Rhode Island. | Courtesy of Glencore
Glencore has been recovering copper and precious metals from e-scrap since the 1980s. But multiple trends are now forcing the world’s largest mining and metals company to adapt to changing markets: a push to decarbonize the transportation sector, efforts to shorten and bolster supply chains, and innovations in consumer electronics design and manufacturing.
Though those areas are shifting fast, the company sees opportunity, particularly in supplying metals for a low-carbon future, said Kunal Sinha, Glencore’s global head of recycling.
“I think the defining trend going forward is going to be the metal demand that’s driven by the transition to a low-carbon future, or to getting to net zero,” Sinha said. “I think battery metals or copper, these are going to be the metals that fuel this transition. … That macro trend is here. It’s going to really support more recycling and the recycling industry, and that’s something I think people should pay attention to.”
Glencore’s Horne Smelter in Quebec was one of the first smelters in the world to recover copper and precious metals from electronic scrap, entering that market in the 1980s. The smelter produces metals from both mined primary feedstocks and from scrap materials. Today, end-of-life electronics and batteries, together, constitute the largest recycled feedstock inputs for Glencore, which receives recovered materials from over 200 suppliers in nearly 40 countries.
The company is currently working to repurpose part of its Britannia Refined Metals (BRM) lead refining facility in England so it can receive, sample and pre-process e-scrap from Europe, he said.
The following is a Jan. 13, 2023, conversation between Sinha and E-Scrap News. It has been edited for clarity and length:
Fitting into public-policy pushes
E-Scrap News: How does Glencore fit into governments’ aspirations to reduce greenhouse gas emissions and shift to alternative energy systems?
Sinha: The first thing to keep in mind is e-waste is one of the fastest-growing waste streams in the world … and the more we can recycle in formal channels, that’s obviously great. We are preventing a potentially hazardous stream from going into landfill, and we are beneficially recovering critical metals from it.
Kunal Sinha
The other thing is there’s a lot of focus on the shortening of supply chains and localizing supply of critical metals. That’s important from a government perspective. Mostly these days those topics are related to energy security or security-of-supply concerns. Very broadly, what we are doing does help because when you are able to recycle more, you are able to recover these critical metals domestically.
So if you are in a region that’s not really well endowed in terms of natural resources, but you still have a lot of consumer products … you already have those metals sitting in these products. So the more we can enable a localized recycling platform, the more we can put those critical raw materials back into the supply chain.
And of course recycling inherently has a much lower carbon footprint. The combination of primary and secondary is arguably the greenest combination, since we are using the combustion of sulfur from primary feed as the source of energy, thereby minimizing the use of fossil fuels in the process.
So you achieve a lot of goals, right? You’re providing those critical metals, you’re shortening supply chains, you’re providing metals with recycled content, with a lower carbon footprint.
E-Scrap News: Looking at the U.S. specifically, how has legislation that drives domestic materials recovery, like the Inflation Reduction Act (IRA), opened new opportunities for Glencore?
Sinha: I think the Inflation Reduction Act has really accelerated the United States’ position in the supply chain for raw materials that go towards electrification or go towards the EV ramp up. If you read it very carefully, they actually look at recycling facilities – as long as you’re doing the recycling domestically and recovering these metals – then these recycling facilities qualify as a producer of those critical metals.
If you take that view, then you are getting a lot of tax incentives, you have access to [Department of Energy] grants and loan schemes. And that really is a major support, and it provides a lot of tailwinds for more recycling. Because outside of the debate on primary mining and how much of that the U.S. can do on its own, now you have a “domestic” source of critical metals, whether it be copper, nickel, cobalt or lithium.
And then we are looking at where and how we can access those benefits. Some of the other companies we have invested in or we work with, they are doing so as well. The other thing I would point out is there is some clarification needed from the Treasury Department on how exactly these incentives would work, so that is coming in March. Once that is clear, then you will see people start to apply it and I think it will be net positive for the recycling business in North America.
“The more we can enable a localized recycling platform, the more we can put those critical raw materials back into the supply chain.”
–Kunal Sinha, Glencore global head of recycling
E-Scrap News: Can you remind me whether metals produced by the Horne Smelter in Quebec would be considered “domestic” under the IRA?
Sinha: When [the IRA] first came out, it defined countries as FTA (free trade agreement) countries and any materials produced or processed there would be viewed favorably. And then the recent guidance basically said that the U.S. government may take a very open view of what an FTA country is. We do have a free-trade agreement with Canada. Once the Treasury guidance comes out, I think it is expected in March … to say the list of countries may be wider than just very strictly FTA – and the FTA itself may be interpreted more generally. So I would think Canada would be viewed favorably in that sense.
Adapting to changing feedstock streams
E-Scrap News: How does your team navigate a changing stream with more plastic and less precious metals?
Sinha: Miniaturization of consumer electronics devices is not a new trend. Form and function is king, and that’s now resulted in wearables. From a cost perspective, OEMs have been trying to engineer-out expensive metals, like gold and PGMs (platinum group metals). So on the one hand you have this trend of consumer electronics becoming smaller and smaller, and probably lower amounts of metal – or cheaper metal – per device.
However, the counterbalancing trends are two. One, there’s a massive push, thankfully, in recognizing that e-waste is one of the fastest-growing waste categories and improving the state of that. We expect collection rates to go up under that pressure. Two, and more importantly, the average consumer is very aware these days of the ESG [environmental, social and governance] footprint of the products they buy. So all else being equal, consumers seem to prefer the company that’s doing the right things environmentally. … And where I’m going with that is if you look at all consumer electronics OEMs, they all have very aggressive targets for recycled content by 2030.
That can’t happen by itself. It means OEMs need to be conscious of designing products that can be recycled, and they really need to work closely with the rest of the supply chain to catalyze more recycling so that we can produce more recycled metal that can meet their goals. I think these trends sort of counterbalance and the net effect, I think, is that the electronics recycling industry has many bright years ahead.
E-Scrap News: From a technical perspective, how does Glencore efficiently recover valuable metals when they’re used in smaller and smaller concentrations in electronics?
Sinha: We are a little different than a standalone recycler or standalone secondary smelter, because Glencore’s approach to recycling has always been that we combine a primary [mined materials] stream and a recycling stream at the same asset. By combining primary and recycling streams, what it does for the recycling businesses is we are able to piggyback on the economies of scale of a massive smelter.
If you look at the CCR (Canadian Copper Refinery), we produce almost 300,000 tons of cathode. The Horne Smelter can process 700,000 to 800,000 tons of concentrates. It’s a massive metallurgical site, which means the unit cost comes down. So our recycling business enjoys that lower unit cost because we can work with the primary side. But the recycling business brings in a lot of precious metals and good-margin business, which helps the primary side. So it’s very symbiotic.
E-Scrap News: As far as supply goes, obviously when you shift to recycled inputs, you’re talking about metals in devices that are spread all over the place. Could you talk about the challenges of collecting that feedstock stream and trying to grow that?
Sinha: One thing I would point out is the contrast between Europe and North America. If you look at Europe, that rate of collection and recycling is probably the highest in the world. It’s north of 40% – certain countries north of 45%. And a big part of that is that the EU took a lot of time some 10 to 15 years ago to put together what’s called the Waste Electronics and Electrical Equipment (WEEE) Directive. Now, there is a lot of government support for that upstream collection of WEEE in Europe, and that has really led to creating a good downstream private sector for electronics recycling, and it has really catalyzed the whole space.
Unfortunately, when it comes to North America, we do not have the equivalent of a WEEE Directive. By my last count, 25 out of the 50 U.S. states did not have an e-waste law. I’m in New York, which does have a very stringent electronics disposal law. So I think there is a role that government has to play in incentivizing collections or disincentivizing improper disposal. And in the absence of that, it’s very difficult for the private sector to come and increase that collection rate. It is very expensive, as you pointed out.
“OEMs need to be conscious of designing products that can be recycled, and they really need to work closely with the rest of the supply chain to catalyze more recycling.”
E-Scrap News: California has a big update, including bringing almost all battery-embedded devices into the program. Do you see that law as helping your e-scrap suppliers produce more material to send to you?
Sinha: First of all, any legislation that encourages more collection and better separation is great. Up until a few years ago, batteries were mostly viewed as a difficult part of the collection ecosystem, because if you don’t handle them properly, they end up causing fires in these recycling companies’ shredders.
I think everyone’s trying to find better and safer ways of separating the batteries and recovering that value. I think the more any state can do to encourage and educate people on those topics and incentivize them to do it, first of all, it’s just great for safety, and then second, that improves the quality of the stream that’s going to any smelter, not just Glencore.
Advice for e-scrap companies
E-Scrap News: How can our readers maximize the financial value that they get from sending material to your company?
Shredded circuit boards at a Glencore sampling facility in Rhode Island. | Courtesy of Glencore
Sinha: I think consistency in the material stream is very helpful. Now we recognize these are post-consumer waste streams. There can’t really be consistency. But we see the better recyclers through their experience and knowledge have figured out a way to look at what’s coming in, segregate it, and create product streams that are more or less consistent within a range. It’s a bit of an art, but many people are able to do it well.
The other thing is we tend to take a more favorable view of working on contracts or deals that are longer term. If there is a longer-term relationship, then you can work on innovative ideas together: creative ways of structuring contracts, looking at new material streams, partnering up on things, possibly even investments.
E-Scrap News: What would you like our readers to be doing five years from now that they’re not doing now?
Sinha: I think recyclers owe it to themselves to sort of get more conscious of their own climate goals and their own carbon footprint. I think there is still a lot of material that gets shipped around a lot farther than perhaps it should, and it adds to that carbon footprint. And while it’s good to say, “Recycling is very good. It’s green,” … if material has to travel 10,000 miles to get processed, is it really that green?
I would hope that suppliers take that broader view beyond just, “What’s my margin and what am I gonna make this month?” But you have to get creative about it, and you have to get collaborative about it, because climate change is a big problem and no one person or one industry or one company can solve it by themselves. In the end, I truly believe that by aligning themselves to these climate goals, in the long term, actually recyclers would be more successful – both economically, as well as with their ESG performance.