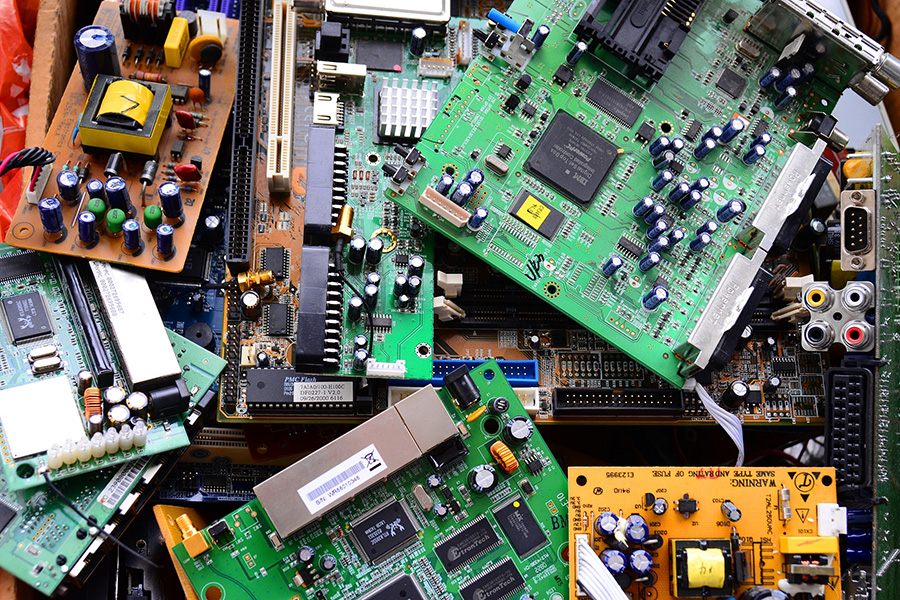
An acid-free dissolution method can selectively target rare earths for extraction. | Bokstaz/Shutterstock
A technology that will allow recyclers to extract valuable metals from e-scrap like shredded hard drives without affecting the other materials is entering its pilot plant stage.
Daniel Bina, CEO of Critical Materials Recycling and TdVib, said the new method will make rare earth recycling more accessible at a time when there is a critical need for more domestic supply.
The method, called acid-free dissolution reaction (ADR), is unique because it can selectively target rare earths and doesn’t use acids to do so, according to Bina. It was developed at the Critical Materials Institute, a federal laboratory, by Denis Prodius and Ikenna Nlebedim, but is being commercialized under a small business called TdVib. Once the testing is completed in August 2023, a new business called Critical Materials Recycling will take ADR to the market.
“It was very important that it was acid-free because that’s one of the major issues with current technology, it uses a lot of acids and that has a lot of issues,” Bina said. Because it is acid-free, ADR is more environmentally friendly and creates less waste and no hazardous waste, he said.
“We can basically recycle a lot of that solution and chemicals we’re using,” Bina noted. “We’re able to recycle them right back into the process and reuse them so that’s been environmentally friendly and helps with economics.”
ADR works by using a specific mixture of chemicals and a selective leaching process to remove the rare earths into a solution, with little to no effect on other materials in the electronics mixture. For example, if used on shredded hard drives, it will not affect the aluminum, copper, gold, silver or other metals. The traditional acid-based method ends up dissolving everything, said Bina, making it impractical.
“Then you have all those elements in solution and it becomes more of a hassle and more of an expense to separate out all the rare earths from the rest, so many actually don’t do that. It’s not worth it,” Bina remarked.
Rare earth magnets make up about 3% of a hard drive, but with ADR they can be extracted, then the rest of the shredded hard drives can be sent through the traditional recycling process.
“We see ourselves in the recycling process that already is in place today, just as an additional step,” Bina said.
While rare earths can be very valuable, right now they are more of a nuisance or contaminant in e-scrap recycling, according to Bina, because they can get mixed in with other components. They are also magnets, and can cause things to stick together when processors are trying to separate out metals.
“In our process, if we’re the first process, where it’s shredded up and then we go through it, when it pulls those rare earths out, the magnet is no longer,” Bina said, putting to rest both the contamination and the magnetic issue.
After the rare earths are pulled out into solution, he said it’s a simple process to drop them out of the solution as a solid. Then, they need a small amount of purification before they can be sold and reused.
Bina estimated that if all the rare earths just from hard drives in the U.S. were recycled, they could provide 25% of all current demand for rare earths in the U.S. And the process doesn’t just work on rare earths in electronics, he added. It can be used on any item that contains rare earths, such as electric vehicle motors.
“The problem here that we’re really addressing and that really makes this process unique – there is no other technology we’re aware of yet today that can pull out these rare earths in a profitable manner from dilute waste streams – is everything else you look at for technology to do this first are going in and manually removing magnets, so they have just magnets, nothing else,” Bina said. “That right there is a huge financial burden to any process.”
Scaling up
The Critical Materials Institute is a U.S. DOE Energy Innovation Hub group, which has laboratories across the country and is headquartered in Ames, Iowa, at Iowa State University.
Bina said TdVib has been the commercialization and business partner for the laboratory for several different projects concerning rare earths, which is how they came to be involved in commercializing the ADR method.
ADR has been in the works for six years. Now, as part of phase two of a federal Small Business Technology Transfer program, the goal is to set up a pilot plant and test out commercial production. Once that is complete, Critical Materials Recycling will take over. While it has some of the same leadership and management, the company is not tied to TdVib in any legal sense, Bina said.
“We’ve been working on it for a while, and taken it from the laboratory and beakers with just a few grams and scaled it up to trying to work just a little larger, but still simple, to now in the pilot plant where we’re using large commercial reaction tanks and such to do much larger volumes,” he said.
Commercial production was scheduled to start in August, but some equipment and supply chain delays have pushed the timeline out. Bina said initial testing to make sure all the systems in the pilot plant are working correctly should begin in September. Once fully operational, the pilot plant will be able to create about 60 tons of rare earth oxides in a year.
The pilot and commercial launch will also help Bina and Critical Materials Recycling determine whether ADR will work better when housed at centralized factories or subleased elsewhere.
The team has already been talking with e-scrap recyclers, Bina said, and the response has been positive.
“Recyclers in general are always looking for any of their value stream they can add to,” Bina said, especially if it’s a fairly simple addition for a high-value material.
“If you can say you’re processing this material and getting five different things, you already have a sixth one there, you just need to extract it,” Bina said. “You just haven’t had the technology to do it yet. That’s kind of an obvious thing to them. They’re already passing something of value through, and were just not taking advantage of it.”
More stories about processors
- New ITAD firm launches, acquiring two processors
- Makor ERP to incorporate ESG reporting into platform
- Australian metals company rebrands, builds Texas plant