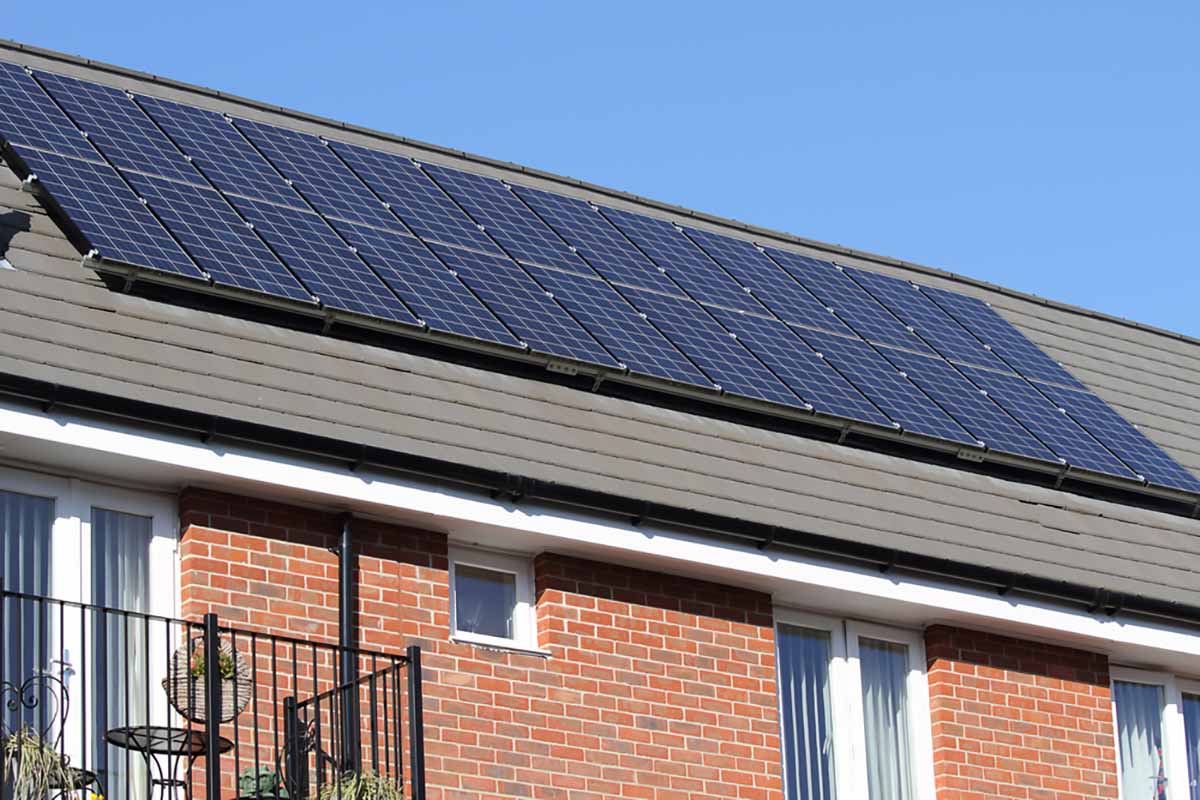
E-scrap processors are developing strategies for an increasing number of PV modules entering the market. | Hill120 / Shutterstock
The challenges of solar panel recycling will sound familiar to e-scrap processors.
The material carries a high cost to recycle properly. Additional factors include limited commodity value, the presence of hazardous metals, a relatively small number of downstream processors and markets working against reuse.
“Solar panels are pretty much the new CRT,” said AJ Orben, vice president of Arizona-based We Recycle Solar.
Interviews with e-scrap and solar panel recycling industry experts shed light on the challenges the sector faces with photovoltaic (PV) modules, which have the potential to be stockpiled, dumped, abandoned, or illegally landfilled.
Partly to head-off potential mismanagement by certified facilities, Sustainable Electronics Recycling International (SERI) is considering adding solar panels to the R2 certification standard. SERI’s R2 Technical Advisory Committee (TAC) will begin the discussion next week.
Meanwhile, more solar panels are continuing to enter the end-of-life stream. Along with processing complications – and the expected additional regulations – are business opportunities, however.
“This is just the tip of the iceberg,” said John Shegerian, co-founder and executive chairman of nationwide electronics processor ERI, referring to the number of panels his company is currently recycling, about a semi-truck trailer full a week. “This is just warm up to the game.”
Complex mix of materials
About 95% of panels sold today are crystalline silicon, which have PV cells made with silicon semiconductors, according to the U.S. Department of Energy. Designed to withstand the elements for decades, solar panels are made up of interconnected PV cells that are encapsulated in plastic and sandwiched between glass and a backsheet. The typical panel has a metal frame, usually aluminum, and external copper wiring.
In an article for E-Scrap News magazine last year, Melissa Ann Schmid of solar power equipment exchange EnergyBin explained that crystalline silicon panels are predominantly made of glass but also contain plastic, aluminum, silicon and copper, along with trace amounts of silver, tin and lead.
Recycling companies can easily separate the aluminum frame and external copper wires for recycling. But because the PV cells are encapsulated in layers of ethylene vinyl acetate (EVA) plastic and bonded to the glass, additional processes are needed to recover the silver, copper or high-purity silicon in the silicon wafers.
Processors taking in solar panels are currently employing different strategies.
We Recycle Solar has a large solar panel recycling plant in Yuma, Ariz., a city on the California border, and a smaller one in New York City. Launched five years ago, We Recycle Solar is recycling tens of thousands of panels each week, with material coming from homes, businesses and solar farms.
The company is the largest recycler of solar panels in the U.S., said Orben, although he noted there’s only a handful of companies recovering the all – or almost all – of the materials in panels.
We Recycle Solar removes the aluminum frame and wiring and shreds the panels. The shredded mix then undergoes secondary chemical processing, electrolysis, and additional processes to separate the metals, silicon and glass for shipments to downstream processors, he said.
“It’s taken us five years to really refine what we do,” he said.
Based in Fresno, Calif., ERI processes solar panels for Redwood Materials, a Carson City, Nev.-based startup targeting recovery of valuable metals from batteries. In April, ERI announced a partnership through which the processor will send all of its recovered batteries and shredded solar panel scrap to Redwood Materials. As part of the agreement, Redwood invested a substantial sum in ERI, according to an ERI press release.
ERI has been working for about three years on R&D for solar panel recycling, Shegerian said. After removing aluminum frames, ERI size-reduces the panels in modified shredders. The key steps in the process are shredding and separating glass from the metals-bearing materials while avoiding unnecessary emissions.
The resulting shredded balls of metals-bearing material are then shipped to Redwood, which uses its technology to separate metals such as copper, silver and lead.
Another e-scrap company processing solar panels is Echo Environmental, which operates a 166,000-square-foot recycling and reuse facility in Carrollton, Texas, near Dallas.
Receiving a million-plus pounds of solar panels a year from manufacturers and others, Echo crews first remove the aluminum frame and clip off wires for recycling, said Tommy McGuire, president of Echo Environmental.
Echo then shreds the modules before using a milling process to separate a portion of clean glass, which is sold for use in fiberglass insulation and reflective paint. The remaining metals-bearing material is mixed into shredded circuits boards from electronics and shipped for smelting.
Complications around ‘hazardous’
Complicating the end-of-life equation is the fact that some types of panels are considered hazardous because of their concentrations of toxic metals. The South Carolina Department of Health and Environmental Control produced a fact sheet listing the different types that may be considered hazardous, noting that non-hazardous panels can be disposed of in municipal solid waste landfills.
Among the types requiring special handling are thin-film cells, which are less common than crystalline silicon panels. First Solar, a solar panel manufacturer that has run a recycling program since 2005, makes cadmium telluride thin-film solar cell modules. According to First Solar, the recycling process involves shredding and milling in a hammermill. After that, the EVA laminate is separated from clean glass. Separately, a third-party company performs a metal precipitation process to recover cadmium and tellurium.
Because of the hazardous metals and additional handling requirements involved, McGuire said Echo advises its customers with cadmium-containing thin-film cells to send them straight to First Solar’s recycling facility in Ohio.
By and large, Echo’s testing shows other panels aren’t hazardous waste, he noted. But that doesn’t mean they should be wasted.
“Your typical PV module doesn’t have a lot of hazardous implications, but similar to electronics, we certainly don’t want them filling up our landfills,” McGuire said.
“The opportunity is massive, but to do it the right way is going to cost a lot of money.” – John Shegerian, co-founder and executive chairman, ERI
Orben of We Recycle Solar said his company’s testing shows that over two-thirds of panels are considered hazardous waste under the federal Resource Conservation and Recovery Act (RCRA) because of their lead or silver concentrations. About 90% of those same panels are considered hazardous under California standards because even if they haven’t exceeded acceptable lead or silver levels, they’ve exceeded state copper or zinc limits.
We Recycle Solar’s Yuma plants has a hazardous waste permit, according to the EPA, which noted that corrosive waste, cadmium, lead and silver are handled there.
In addition to the hazardous material considerations, recycling solar panels presents challenges in terms of economic viability.
“Current technology, infrastructure, and processes associated with recycling PV modules are not optimized for cost-effective recovery of high value materials,” according to a March 2021 report from the National Renewable Energy Laboratory (NREL) and the Electric Power Research Institute. “As a result, the cost of recycling is often outweighed by cheaper more accessible disposal options.”
Solar panel processors must charge fees to accept solar panels to offset their processing costs.
Orben said We Recycle Solar spends up to $25 per panel in processing costs to yield between $2 and $4 in value from aluminum, copper, lead, glass, silver and silicon. OEMs have lightweighted and used less valuable metals in newer generations of more-efficient products, which is great news from the manufacturing and consumer perspectives but not for recyclers, he said.
Meanwhile, Orben doesn’t foresee processing costs coming down significantly in the future as a result of economies of scale. A lot of the costs will still be tied to labor, which is only expected to become more expensive.
He noted that there remains a financial incentive for waste generators to pay to recycle panels when the alternative is hazardous waste disposal, but that leverage slips away when cheaper municipal solid waste landfills are an option.
Additionally, not all collectors understand the economics of properly handling the material, Orben noted, creating cost pressures from the outset.
We Recycle Solar frequently gets calls from transfer stations, landfills and other recyclers that have accepted solar panels at no cost or low cost (such as 10 cents a pound) because they think they contain a lot of valuable materials.
McGuire of Echo Environmental added that solar panel commodity value is predominantly in the aluminum frames, with the wires and clean glass product also generating some amount of revenue.
Echo’s process of mixing shredded PV cell material with shredded circuit board scrap that’s shipped to a smelter reduces the value of the circuit board mix by several cents per pound, but the practice also keeps the material out of landfills, allows metals to be recovered and offsets smelters’ needs for fluxing agents, he said.
ERI’s Shegerian noted that, for now, his company’s Fresno plant is the only ERI facility processing solar panels. But ERI’s other facilities across the country are getting calls about solar panel recycling on a daily basis
“The opportunity is massive, but to do it the right way is going to cost a lot of money,”Shegerian said.
Resale market headwinds
Solar panels are designed to produce electricity for decades, so reselling a used panel may appear the best option economically and environmentally, and that exchange does happen.
At the same time, processors said, certain market and tax policy forces are also working against reuse.
McGuire said Echo has the ability to test the energy output of used panels so they can be resold. That works well for higher-value modules, he said, noting that there are international markets for secondhand modules, as well as one-off domestic projects.
But panels that didn’t pass manufacturers’ quality control checks can’t be resold, he noted. And when contractors perform de-installs and aggregate and ship solar panels to Echo, what arrives is often a mismatch of different types of panels, making it tough to keep a consistent inventory, McGuire said.
“Current technology, infrastructure, and processes associated with recycling PV modules are not optimized for cost-effective recovery of high value materials. As a result, the cost of recycling is often outweighed by cheaper more accessible disposal options.” – A March 2021 report from the National Renewable Energy Laboratory (NREL) and the Electric Power Research Institute
Additionally, the pace of panel innovation hampers resale because prices for new panels have come down in line with efficiency boosts. According to the U.S. Energy Information Administration, the average value of PV modules shipped in 2019 (the most recent year for which data is available) was 41 cents per watt of electricity generated at peak performance. A decade earlier, the average was $2.79 per peak watt.
We Recycle Solar does resell solar equipment. But Orben also likened the problem to that facing some segments of the electronics market. “Having a 15-year-old panel that still produces is a lot like having a Pentium 3 today,” Orben said.
Further holding back the secondary market is U.S. tax policy. McGuire noted that the federal government provides tax credits for homeowners installing new PV systems – for 2021, the credit is 22% of the cost of a system.
“It’s really an uneven playing field, because you can’t get that tax credit on secondhand modules,” McGuire said.
Enter the regulations
More solar panels are expected to enter the waste stream in coming years.
According to the U.S. Energy Information Administration, shipments of new panels have increased substantially over the past 15 years. In 2019, enough PV modules were shipped to produce over 16 million peak kilowatts of electricity, a nearly 14-fold increase over the amount shipped a decade earlier.
Many of them will be decommissioned well before the end of their usable lives, because of performance improvements and lower costs for new panels (Shegerian of ERI said power producers may replace them in five years or less because the ROI is so compelling).
A report from the International Renewable Energy Agency (IRENA) and International Energy Agency Photovoltaic Power Systems Programme (IEA-PVPS) estimates that, by 2050, cumulative global PV panel waste will have reached 60-78 million metric tons, up from about 43,500-250,000 tons in 2016.
The report calls for the passage of PV-specific waste regulations, among other measures. Some of that has already occured. For example, Europe has adopted laws forcing solar panel producers to finance the collection and recycling of their products.
“I think it’s very counterintuitive to the entire mission of solar if that stuff ends up in a landfill.” – Tommy McGuire, president, Echo Environmental
In 2017, Washington state became the first state to pass a bill establishing an extended producer responsibility (EPR) program for solar panels. Starting in July 2023, the law will require manufacturers to fund collection and recycling of the panels.
In California, the Department of Resources Recycling and Recovery (CalRecycle) has considered adding solar panels to its electronics recycling program. The department is working with other branches of state government to draft a paper, expected to be released this year, on end-of-life management of PV panels.
In the meantime, the California Department of Toxic Substances Control (DTSC) late last year approved regulations (which were based on 2015 legislation) classifying PV modules as a universal waste, not a hazardous waste, easing regulatory burdens associated with collecting and shipping them. That being said, the panels are still considered hazardous if testing shows they exceed hazardous metals concentration limits in California or federal law, and universal waste handlers are required to do that testing when they discard the panels.
McGuire of Echo said he’d like to see regulations lead utilities to build the cost of recycling into their solar projects. Echo receives a lot of broken or defective panels from manufacturers, but he has yet to see a million pounds come in from a solar farm decommissioning/replacement project, he noted.
“I think it’s very counterintuitive to the entire mission of solar if that stuff ends up in a landfill,” he said.
Set to be integrated into R2?
Meanwhile, SERI is looking to add solar panels to the R2 recycling standard, a step that would provide clear guidelines and requirements for e-scrap companies looking to handle the material.
After the newest version of the standard, R2v3, was finalized in 2020, SERI formed a workgroup of solar industry stakeholders to look at the issue. Among the 24 members of that workgroup were Dwight Clark of We Recycle Solar and Echo Environmental’s McGuire, who helped lead the group.
That workgroup met for six months before presenting its conclusions to the TAC, which will begin considering adding PV modules on May 19. The TAC meeting isn’t open to the public, but stakeholders can email their comments on adding PV modules to R2 to info@sustainableelectronics.org.
If the TAC decides to pursue adding PV modules, SERI would add new solar panel industry stakeholders to the TAC. The standard language could take two-plus years to draft and finalize.
Corey Dehmey, SERI’s executive director, noted that R2v3’s new structure allows for the addition of appendices for specific materials. A new solar panels appendix would be mandatory for R2-certified companies taking in PV panels, he said.
“[Adding PV modules would be] giving the world a way to recognize processors that are handling them in an environmentally sound manner,” Dehmey said in an interview. “Processors are going to tell you they’re handling them right. How do you know?”
Dehmey noted that the NSF/ANSI 457-2019 standard has been created to cover the life cycle of PV modules and that the Global Electronics Council has adopted that standard for its EPEAT-listed products. But there isn’t a standard focused specifically on end-of-life recycling.
McGuire said the adding PV modules to R2 would help ensure certified facilities send solar panels – or residuals from them – to proper downstrams.
Shegerian was also supportive. ERI’s facilities are certified to both R2 and e-Stewards.
“It’s always helpful when more certifications come in and help put guardrails around what really the word ‘responsible’ is,” he said.
More stories about markets
- Pulse Supply Chain opens Dallas repair, recovery facility
- Iron Mountain sees ITAD surge, raises forecast on record Q2
- E-plastics recycling company expands product line