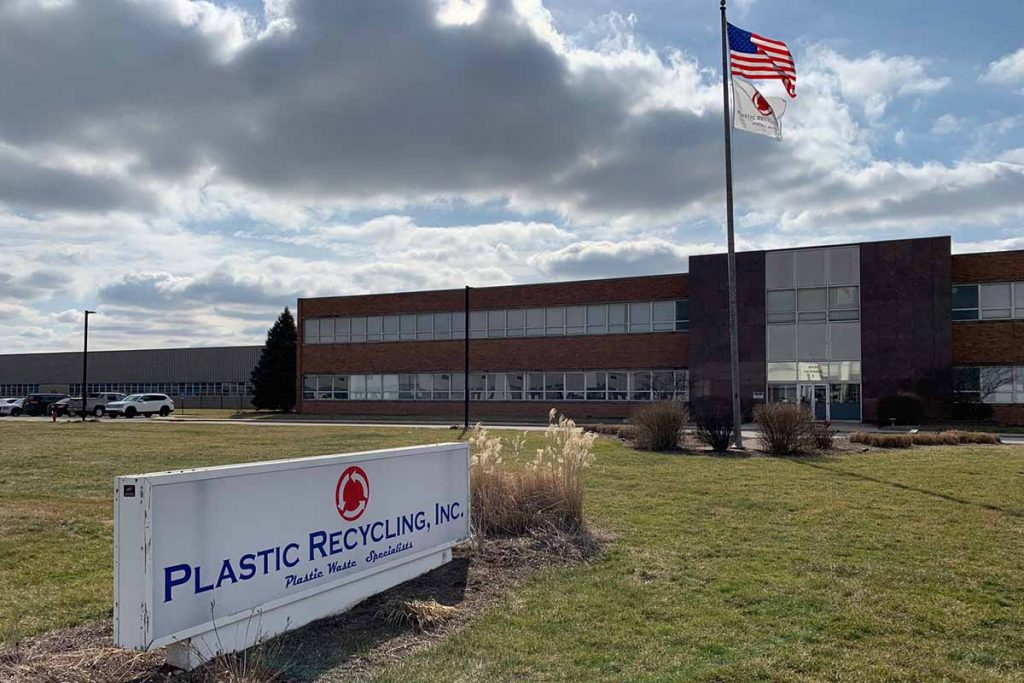
Plastic Recycling, Inc. is the latest company to open North American capacity for e-plastics. | Courtesy of PRI
Indianapolis-based Plastic Recycling, Inc. has expanded with a project that underscores the opportunities and complexities in recycling plastics from scrap electronics.
PRI invested roughly $2 million to install a system that produces clean recycled flake from e-plastics, Brandon Shaw, PRI’s marketing manager, told Resource Recycling. The material is sorted by polymer.
PRI is processing the polyethylene/polypropylene (PE/PP), acrylonitrile butadiene styrene (ABS) and polystyrene (PS) flakes into plastic pellets. Most of the pellets will be sold, but some will be molded by a PRI-owned manufacturer into plastic cores for paper rolls.
“Our end goal is to recycle this stuff – breathe new life into it – and sell it back to [original equipment manufacturers],” said Josh Barrick, who oversees marketing and purchasing for PRI. “Also, it would be very, very nice to get it back into electronics.”
Trend of domestic investments
PRI is the latest company to open North American capacity for electronic scrap plastics, which have typically been exported to Asia but are now facing tightening global trade regulations because of an amendment to the Basel Convention on the Control of Transboundary Movements of Hazardous Wastes and Their Disposal.
The Basel changes went into effect Jan. 1, and countries around the world are now looking to pass the trade provisions into their own national laws.
Even before the Basel amendment, China’s scrap imports crackdowns – first Green Fence and then National Sword – threw export markets for e-plastics in disarray.
A number of North American companies are seeing opportunities. Over the past several years, China’s restrictions helped spur Canadian recycling companies FCM Recycling and BoMET Polymer to invest in e-plastics recycling capabilities.
More recently, electronics recycling companies eCycle Solutions and Universal Recycling Technologies (URT) installed e-plastics sorting systems, and BoMET Polymer installed additional e-plastics sorting equipment. Meanwhile, RePolyTex, a plastics reclaimer and product manufacturer, is now producing construction boards from shredded e-plastics, and chemical recycling company Brightmark Energy is sourcing e-plastics for conversion into chemical products such as fuels and waxes.
In business for over three decades, PRI has long been known as a recycler of various plastic streams, including rigid and foam polystyrene. Shaw explained that PRI was motivated to move into e-plastics partly by market opportunities opened by the Basel amendment and partly because PRI needs the feedstock for its extruders to meet demand for recycled plastic.
Creating clean, sorted flakes
The e-plastics system was installed in Indianapolis at PRI’s 120,000-square-foot facility, where the company has an existing scrap polyolefins processing line.
The line was first put in place in March 2020, and PRI began testing it in July, Barrick said. The system consists of three float-sink tanks, where materials are sorted based on their density. The process also uses a proprietary technology that removes labels, rubber and other contaminants as well as an electrostatic separator, which can sort PS from ABS plastics.
Finally, the line uses one flake sorter, which sorts by color, and six dryers.
The tanks use density-modified water, which allows them to make separations that would not otherwise be possible. The tanks remove metals, plastics that contain fire retardants, and other contaminants.
The system input is shredded e-scrap and toner cartridge plastics (the material is shredded again before going into the first of the tanks). The output consists of black, gray and white flakes of the following polymers: PE/PP (mostly PP), ABS and PS.
In addition to generating shredded plastics, many electronics recycling companies produce bales of e-plastic from the manual dismantling of CRT TVs and monitors. Those plastics components contain more flame retardants, however, reducing their recyclability in the U.S. As a result, PRI isn’t taking in baled e-plastics from those sources.
Vertically integrated company
The flakes that PRI produces are shipped to the company’s 500,000-square-foot location elsewhere in Indianapolis, where blending, compounding and pelletization occurs. PRI’s five single-screw extruders and two twin-screw extruders have a total throughput capacity of 120 million pounds per year.
Shaw estimated 85% of the e-plastics pellets will be sold, and the remaining 15% will be transported back to the sortation facility, where PRI’s manufacturing arm, Recycling Technologies, Inc. (RTI), will mold PS into plastic cores for paper rolls, such as those holding sales receipt paper.
Barrick highlighted the company’s level of vertical integration as particularly noteworthy.
“It’s unique because there are places that do parts of what we do, but they don’t do all of it,” he said.
Shaw and Barrick said the Basel amendment has opened up a market opportunity, but uncertainty remains. Barrick noted that a lot of e-plastics generators have been “drunk off export pricing,” so PRI is waiting to see how the market pans out.
Shaw said PRI plans to add capacity to its e-plastics system, as needed. For a minimal additional investment, the company could double the line’s capacity, he said.
A version of this story appeared in Resource Recycling on January 26.
More stories about e-plastics
- LG collection volume increased notably in 2024
- Malaysia to fully halt US e-plastic imports
- E-plastics recycling company expands product line